When teams first look into implementing a digital inspection platform, a few predictable questions pop up. What will it cost? Is it secure? How long will it take to train my team?
These are fair questions, but they only scratch the surface.
To unlock the full value of a digital inspection platform like Inspectivity, it helps to ask more strategic questions. Questions about flexibility, scalability, future-proofing and team empowerment.
In this article, we answer both the Frequently Asked Questions (FAQ) that we hear all the time, but more crucially, all the “Should Ask Questions” (SAQ) that forward-thinking teams are using to drive successful digital transformations.
The FAQs – Straight Answers to Common Concerns
What does Inspectivity offer that ERP systems don’t?
ERP systems are great at managing work orders, but they’re not built for inspections. That’s where Inspectivity comes in.
We provide a purpose-built, mobile-first inspection platform that captures high-quality data directly in the field. It connects inspection outcomes to your asset hierarchy and makes collaboration faster and easier without relying on spreadsheets, PDFs, or manual uploads.
Whether you’re managing day-to-day inspections or major projects, Inspectivity fills the operational gap left by traditional ERPs.
We’ve used enterprise software before. Is it expensive?
Not in the way you might expect. Inspectivity is a cloud-based SaaS platform with no infrastructure cost and a flexible pricing model based on your subscription tier and usage.
Most customers can get started without any custom development. However, optional development costs may arise if you need advanced integrations, tailored reports, or bespoke workflows. The good news is that Inspectivity is designed to accommodate this. Unlike many platforms, we support customisation where it counts.
Whether you need to match a specific reporting format, integrate with your internal systems, or automate engineering calculations, our platform can adapt to your requirements.
Our customers often see 25% to 50% man-hour savings across inspection lifecycles, an immediate and measurable benefit. But the true value goes beyond hours saved.
Inspectivity improves collaboration between the field and office, standardises how inspections are carried out, and produces consistent, high-quality data. That structured data unlocks downstream opportunities for AI, automation, and advanced analytics: capabilities that simply aren’t possible with paper or spreadsheet-based workflows.
Better inspection data also leads to better engineering decisions. When issues are identified and addressed earlier, downtime is reduced. And that matters. A recent industry report we shared highlighted that unplanned downtime can cost as much as AUD $349,000 per hour.
Read more about the cost of downtime
Compared to traditional enterprise platforms with big CapEx spends and heavy IT overhead, Inspectivity delivers a compelling combination of speed, insight, and long-term return on investment.
How do I know your software will meet our information security requirements?
Security is built into the fabric of our cloud inspection software, the infrastructure, as well as the operational processes we use to deliver best-in-class industrial solutions. You can rest assured that your data is safeguarded.
Inspectivity hosts the Inspectivity Platform for its clients “in the cloud”. We have a long-standing association with Amazon Web Services (AWS), which includes formal membership of the AWS Partner Network (APN). The APN offers many benefits, such as access to the AWS Foundational Technical Review (FTR). FTR is an AWS-managed audit function that ensures SaaS providers follow AWS Well-Architected practices, awarding the “AWS Qualified Software” status only for solutions adhering to the strictest standards.
Furthermore, Inspectivity is certified to ISO 27001 and ISO 9001 quality and information security management system standards. Our security policy mandates that a consistent, risk-based approach is implemented for information security to maintain information confidentiality, integrity and availability.
Inspectivity’s Quality Information Management System is independently audited and certified by 3rd parties. Copies of certificates of compliance are available on request.
Are user actions fully auditable and traceable?
Yes. All user access to the Inspectivity Platform is through named accounts, meaning every action is linked to a specific individual. Whether someone creates an inspection, updates an issue, or edits asset data, the platform records who did what and when. This ensures accountability and provides a full audit trail across inspections, items, modules, and user sessions. Audit logs are available throughout the platform to support compliance, investigations, and internal governance.
Where is my data stored, and can I export my data?
Inspectivity uses AWS data centres that are geographically close to the client, and your data remains your intellectual property. It is kept confidential according to the terms and conditions set out in our terms of use. This includes asset and inspection data, your reports, and configurations, entered into or produced by the Inspectivity Platform.
Exporting data is easy through the available functions in the Inspectivity Platform’s web interface.
How long will this take to implement?
We’ve seen full implementations for major Tier 1 organisations in under four weeks. That’s possible because Inspectivity is a no-code platform designed for fast onboarding, and we support you every step of the way.
Via optional Professional Services, our teams can work with your internal stakeholders to quickly configure your first inspection use case. We can provide best-practice guidance on asset hierarchy, form design, workflows, and role permissions. From there, we can help you prepare for future phases of rollout.
Most customers start with one inspection workflow, such as mechanical or electrical inspections, however, Inspectivity’s power is the flexibility to support multiple use cases across your organisation. Once live, it’s easy to expand to shutdowns, QA/QC, asset integrity, maintenance inspections, and more, all within the same platform.
How long will it take to train my team to use it?
Inspectivity’s apps (Portal and Go) are designed for field teams and engineers, not software developers.
Most users are productive within a few sessions. For power users and admins, we can offer structured training and detailed online documentation is always available. We also provide concierge services in addition to standard support for enterprise clients. For day to day users our web and mobile apps are intuitive. Typically getting started with minimal guidance.
How many people will it take to install in my business?
You don’t need a battalion of consultants.
We recommend that our customers nominate a focal point within their team to lead the implementation. This is typically an engineer, inspector, or digital champion who understands the inspection process and can coordinate internally. The focal point acts as the primary liaison between your business and Inspectivity, helping to ensure alignment, share sample data, and guide configuration decisions.
From there, a small group can configure templates, import assets, and roll out a pilot using Inspectivity’s no-code tools. If needed, our Professional Services Team can provide direct support to streamline configuration, deliver custom training, and prepare your team for scale.
This approach keeps internal effort lean while still allowing your implementation to move quickly and with confidence.
How do I know it will work?
We encourage free trials and paid pilots so you can validate Inspectivity in your environment before scaling up.
A commercial pilot typically means selecting a specific inspection use case, configuring the relevant asset models and templates, and running real inspections with your data and team. It’s a practical way to test the platform’s fit, ensure workflows align with your needs, and gather feedback before committing to a broader rollout.
With hundreds of successful use cases across engineering, energy, mining and infrastructure, Inspectivity is field-tested and proven. You’ll know it works because you’ll try it with your real assets, your data, and your inspection team.
Will it work with my existing IT systems?
Yes. Our REST API and “webhooks” allow integration with ERPs, asset management systems, and other enterprise tools. For example, you can sync inspections with work orders or extract structured data for BI dashboards.
Even if you’re not ready to integrate straight away, Inspectivity can operate as a standalone system and export/import via Excel, making staged integration easy.
Who in my industry is using this already?
Inspectivity is used by Tier 1 operators, engineering service providers and asset owners across the globe. We support large and small businesses alike and have price plans to suit.
Our clients include teams in energy, resources, infrastructure and renewables, many of which operate in regulated, high-consequence environments. The platform supports both daily maintenance tasks and major capital project completions.
In which industries is this being used successfully?
Inspectivity is proven in:
- Oil & Gas (onshore, offshore)
- Mining & Resources
- Chemicals & Manufacturing
- Infrastructure & Transport
- Engineering & EPCM services
If your work involves inspecting assets for compliance, safety or performance, then this platform is a perfect fit.
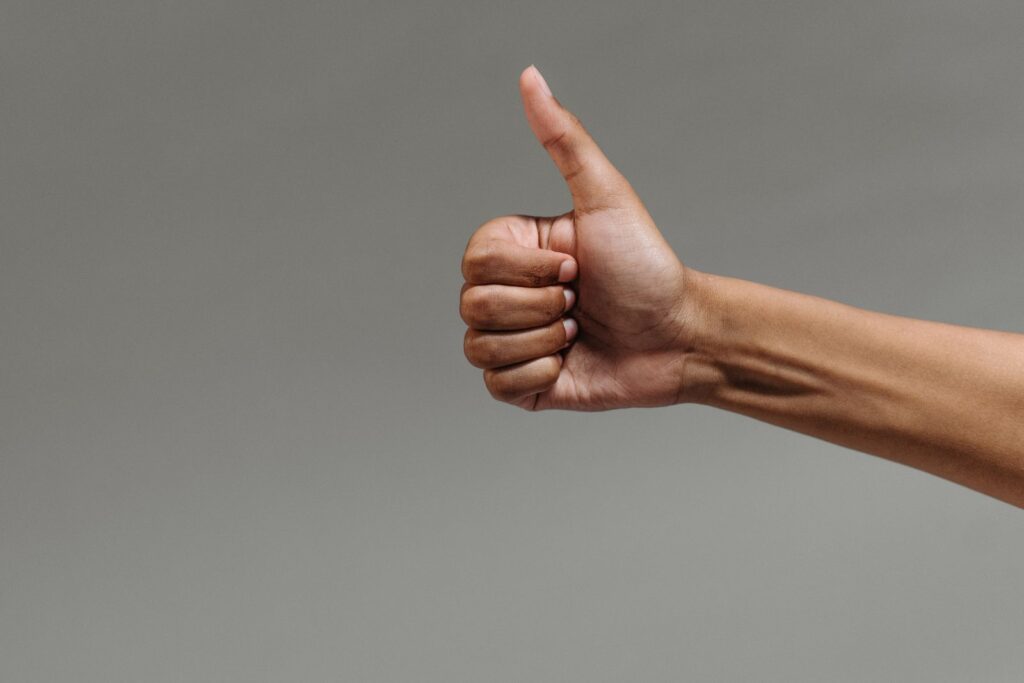
The SAQs – Questions That Actually Drive Value
The questions below go beyond the usual software checklists. These are the strategic questions that smart teams are asking to unlock long-term value from their inspection platform. They help uncover opportunities for scalability, control, and smarter decision-making.
Can we expand the use and application of your software to other teams in the future?
Absolutely. Start with one use case, then scale.
Our customers often begin with inspections for one team, then expand usage to operations, shutdowns, commissioning, QA/QC, or third-party contractors. All your inspection templates and asset models live in one platform, making expansion seamless.
Can we store the inspection history against the asset?
Yes. That’s the core design principle of Inspectivity: it’s asset-centric.
Every inspection, issue, photo, comment and signature is stored against the asset in your hierarchy. That means your inspection history isn’t buried in PDF archives. Instead, it is structured, searchable, and ready for analytics.
Can I reinspect an asset with previous inspection data available in the field for comparison?
Yes. Field teams using Inspectivity’s Go app can access previous inspection results, issues, and photos, even when offline. This is particularly useful in remote or offshore environments where network connectivity is intermittent or unavailable.
You can also configure the inspection template to carry forward data from earlier inspections, such as measurements, comments, and issue statuses. Alternatively, you can require inspectors to review and close out existing issues before they can proceed. This ensures continuity, supports better decision-making in the field, and reduces the risk of repeating work or missing critical findings.
Do you have smart forms that can adjust to the type of inspected asset or use case?
Yes. Our form builder supports conditional logic, field dependencies, multi-selectors, and reusable text snippets. You can configure a single smart template to behave differently based on asset type, location, or risk rating. This means you can create highly flexible inspection templates that adapt automatically to different operational contexts. Whether you’re inspecting a pressure vessel, an electrical panel, or a pipeline segment, the form can adjust to present the right checks, calculations, or required photos. This streamlines data capture and helps reduce configuration overhead.
Can I implement complex engineering calculations out of the box?
Yes. Our forms support JavaScript customisers, allowing you to build smart automation and calculations directly into inspection templates or issue types. This gives you the flexibility to implement engineering logic such as design tolerances, conditional fail states, or calculated fields like pressure ratings or corrosion rates. It means engineers can embed technical rules into the form logic itself, allowing the platform to guide inspectors through complex evaluations without requiring external software or manual calculation. No external app or coding team required.
Can I support complex or custom inspection workflows?
Yes, Inspectivity is designed to support complex inspection processes, even in highly regulated or technically demanding environments.
You can configure form behaviours, manage use case-specific review transitions and control user interaction with workflow statuses via our powerful security model. All directly via the no-code interface.
For more advanced workflow requirements, such as multi-stage reviews, conditional approvals, or tailored status transitions, our team can implement these via optional workflow customisers.
These capabilities allow you to tailor inspection behaviour to your exact process.
Can I give my customers real-time access to their data?
Yes. You can create read-only user accounts, configure dashboards, or share live registers filtered by project, asset, or role. This is particularly useful for engineering service providers who want to keep teams and clients informed and demonstrate value in real time.
Complimentary read-only access is included with some of our subscription tiers. The Professional tier supports up to 20 read-only users, while the Enterprise tier includes unlimited read-only access.
Can I make sure my users only have access to the data and functionality their role requires?
Yes. Our role-based security model lets you tightly control who can create, view, edit, or approve data across every phase of the inspection lifecycle. You can configure access based on project, asset, role, or team discipline, ensuring that each user sees only what’s relevant to their responsibilities. You can also hide specific tabs, restrict certain form actions, or lock down issue types and inspection templates based on seniority, location, or function. This ensures compliance, data integrity, and a simplified user experience for every stakeholder.
Are you ISO certified?
Yes. Inspectivity is certified to:
- ISO 27001 (Information Security)
- ISO 9001 (Quality Management)
These certifications cover both the platform and the way we operate as a company.
Inspectivity also has a long-standing association with Amazon Web Services, which includes formal membership of the AWS Partner Network (APN). The APN offers many benefits, such as access to the AWS Foundational Technical Review (FTR). FTR is an AWS-managed audit function that ensures SaaS providers follow AWS Well-Architected practices, awarding the “AWS Qualified Software” status only for solutions adhering to the strictest standards.
Can I create an asset, perform an inspection or raise a corrective ad hoc offline in the field?
Yes. Inspectors using the Go mobile app can create new assets, raise inspections, and record issues completely offline. This gives field teams full flexibility in remote or disconnected environments. The app stores all asset hierarchy and inspection data locally, then allows the user to sync with the cloud once connectivity is restored, ensuring continuity and data integrity. This approach eliminates data loss, supports timely decision-making, and ensures your records are always up to date, no matter where the inspection takes place.
Can I take a photo or a video offline in the field?
Yes. Inspectors can capture rich media such as photos, videos, and audio recordings directly within the Go mobile app, whether online or offline. Media is always recorded in context, linked to a specific form field, issue, or asset. When working offline, all files are stored locally and synced to the cloud once connectivity is available. This ensures accurate and complete records, even in remote environments. Most importantly, all media is “highly labelled” automatically.
Can I integrate QR codes or RFID?
Yes. Inspectivity supports the use of QR codes and RFID tags to identify and access assets quickly in the field. Scanning a code or tag using the Go app instantly pulls up the relevant asset and inspection history, reducing manual search time and minimising errors. This is especially useful in environments with large volumes of equipment or repetitive inspections.
For RFID, Inspectivity supports passive high-frequency (HF) RFID tags using Android devices with NFC capability. External RFID readers can also be used if they connect to the device as a Human Interface Device (HID), such as through a Bluetooth reader that simulates keyboard input.
Can I connect my business intelligence tools to the data?
Yes. Inspectivity provides access to real-time, BI-optimised views of your inspection data. This enables you to connect and analyse data using a wide range of business intelligence tools, including Power BI, Tableau, Cognos, Qlik, Domo, and Looker.
For Power BI specifically, we offer additional support through a baseline PBIX file with a prebuilt data model. Power BI dashboards can also be embedded directly into the Inspectivity Platform, or you can embed any HTML-based dashboard for seamless access alongside your inspection workflows.
For clients who prefer ready-to-use insights, the Inspectivity Platform also includes built-in operational dashboards, providing real-time visibility into inspection progress, asset status, and issue trends without additional setup.
Can you set the Inspectivity Platform up for me?
Through our Professional Services, Inspectivity can assist clients in configuring digital inspection use cases that follow best practices for our technology and allow clients to lay the foundation for an intuitive and scalable implementation.
We can assist with configuration and provide bespoke training to your teams. We can customise the software for specific requirements and assist with integration to your internal systems.
Our focus is on the delivery of asset-centric digital inspection management in the energy, engineering, resources and asset management sectors. We understand the complexity of these projects, the likely data volumes and how this translates to software delivery. Why not leave us to do the heavy lifting?
Wrapping Up
Digital inspections can do more than save time. They can transform the way you manage critical assets, collaborate across teams, and leverage data.
But to get there, you need to look beyond the basics. The most successful Inspectivity customers are the ones who ask deeper questions. About inspection history. About scale. About security and integration. About who else needs access to the data, and why that access matters.
If you’re ready to move beyond paper checklists and static PDFs, we’re here to help.
Get in touch with Inspectivity or start a free trial today. You’ll be surprised how quickly “What if?” becomes “What’s next?”