Client Goal
SKN enhance offshore execution and overall compliance of Electrical Equipment in Hazardous Area (EEHA) inspections for Australian oil and gas operator.
Problem
Oil and gas operator with a large volume of inspections non-compliant and overdue according to AS/NZS 60079-17 for one of their offshore floating production, storage and offloading vessels.
Solution
Enhance offshore execution and overall compliance of EEHA inspections for Australian oil and gas operator.
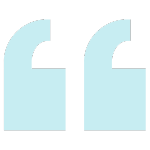
Inspection man-hours have been reduced by 50%, resulting in a $750,000 saving during the first 3-month inspection campaign.
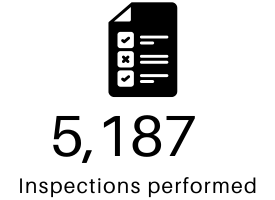
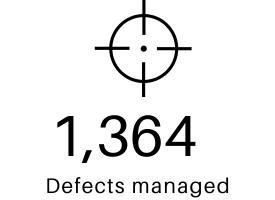
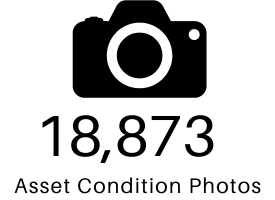
Challenge
Hazardous area compliance is a key performance standard requirement for oil and gas operators but without effective execution strategies and automation, it can often lead to an overwhelming situation with unacceptable legal and safety risks. SKN’s client had reached such a precipice.
Stephen Vanderdeyl, SKN’s Engineering Director explains that a short-term recovery plan combined with an improved execution strategy was required. Over 45% of the vessel’s EEHA equipment was overdue for inspection and the existing ad-hoc paper-based process was not suitable to sustain a recovery and improved future process.
- Non-compliant & overdue AS/NZS 60079-17 inspection requirements.
- Equipment inspections scheduled on an ad-hoc basis dependent upon compliance date.
- Lack of EEHA Planned Maintenance Routines (PMRs) in the Computerised Maintenance Management System (CMMS).
- Manual and complex status reporting with low data quality.
- Lack of real-time visibility of progress and status.
- Paper-based Inspection and Test Record (ITR) process.
- Standard inspection strategy for Close (90%) and Detailed (10%) inspections.
- Multiple data sources for EEHA status and technical information.
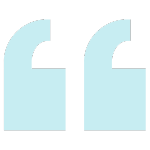
Although the priority was to overcome non-compliance, there was a clear opportunity to improve an array of existing processes, most notably enhancing the execution of inspections in the field with the use of a digital inspection solution.
SKN’s Engineering Director, Stephen Vanderdeyl.
Solution
SKN identified the immediate challenge as the high volume of non-compliant inspections. The existing paper-based process was inadequate for an urgent recovery. A digital inspection management system was essential to streamline the process, automate reporting, and establish a foundation for an enhanced EEHA execution strategy.
The client entrusted SKN with the implementation of the Inspectivity Platform, a digital inspection SaaS product, to create a paperless ecosystem and quickly restore compliance for the offshore operator. Inspectivity’s cloud inspection management software, integrated with a mobile app, features a robust asset-centric model that aligns perfectly with the client’s work order management systems, providing standardised inspection and issue management workflows.
Analysis and Configuration
As with any enterprise software implementation, the initial phase involved detailed analysis. This included reviewing available documentation and gathering information from stakeholders about existing workflows and role-based actions. The outcome was the development of swim lane diagrams/business process maps to thoroughly document the existing processes. These diagrams identified data flows between field activities and source systems like the CMMS, pinpointing current bottlenecks and inefficiencies.
In light of the Inspectivity Platform SaaS solution, the next stage involved remodelling business processes to create revised swim lanes and more efficient workflows. These revised workflows served as the basis for user acceptance of the new processes.
The analysis phase, performed by SKN and Inspectivity consultants, also developed the asset and inspection models needed for configuration:
- Hierarchy structure, asset identification/classification and technical data
- Inspection, Issue and Assessment form layouts
- Security role scheme
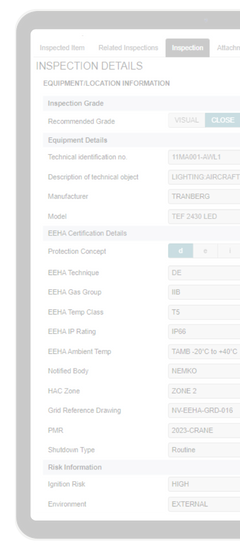
Hosting
Inspectivity hosts the Inspectivity Platform in the cloud, leveraging a mature technical infrastructure and server configuration that follows industry best practices. Amazon Web Services (AWS) is used to provide this technical infrastructure, offering highly reliable and scalable cloud computing services.
Key benefits include cost savings, increased speed and reliability, advanced information security, and significantly faster setup compared to on-premise solutions.
Training & Support
To support multiple offshore and onshore teams, SKN and Inspectivity developed a bespoke training plan delivered through classroom-based sessions. Additionally, SKN provided offshore leads operating in a train-the-trainer capacity, while also providing a senior focal point onshore for remote domain support.
Software-related support is provided by the Inspectivity team based in Perth, Australia.
Results & Benefits
With the collaboration between SKN and Inspectivity, the oil and gas operator now benefits from a significantly enhanced EEHA management delivery model. Key achievements include:
- Development of a Risk-Based Inspection Execution strategy.
- Organisation of a module/area-based, structured 4-year inspection campaign.
- Implementation of a digital inspection solution with ex-rated hardware.
- Automatic Master Data update exports and streamlined updates.
- Availability of a Digital Certificate Library during inspections.
The value for the customer is substantial. Teams can now collaborate on compliance status with access to live inspection data. The previous static approach has been transformed to support real-time interventions, enabling issues to be resolved more quickly. Inspection man-hours have been reduced by 50%, resulting in a $750,000 saving during the first 3-month inspection campaign. Further cost savings have been realised due to decreased administrative tasks and improved productivity through a module-based execution strategy.
Inspectivity’s collaboration with SKN in delivering EEHA excellence to this customer has exceeded expectations.
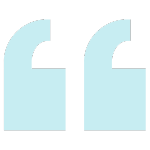
The advanced technological capabilities of Inspectivity coupled with the technical expertise of SKN around EEHA management has provided a real success story with this particular scope. The collaborative approach with our client has resulted in real, measurable efficiency gains and a “best in class” EEHA solution.
SKN’s Engineering Director, Stephen Vanderdeyl.
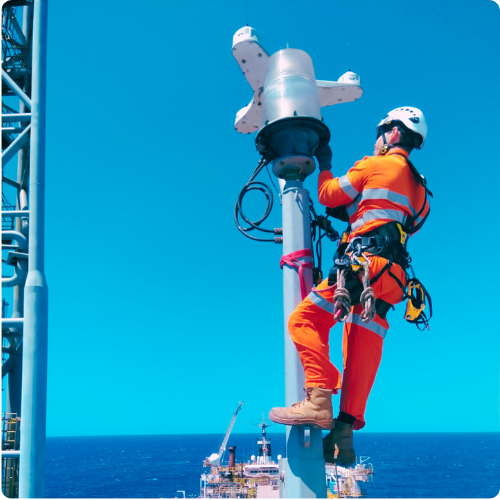
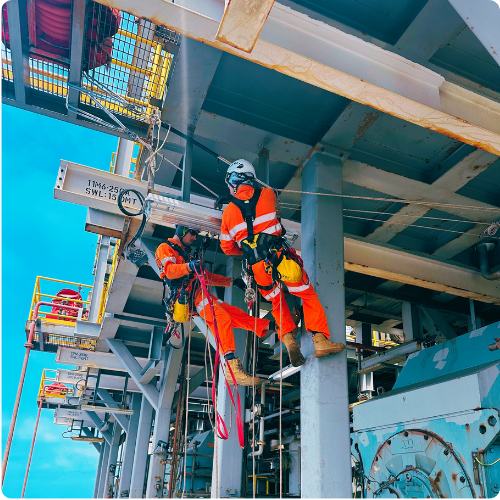
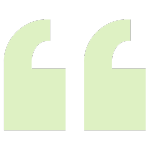
SKN’s technical and engineering expertise combined with Inspectivity’s cloud inspection solutions provide a cookie-cutter approach that we can apply to any customer struggling with hazardous area management. This service ensures operators of critical infrastructure are audit-ready and critical safety issues are highly visible to the team. Given recent changes to industrial manslaughter laws we feel this solution provides comfort to the teams involved.
Paul Eddison, Inspectivity co-founder
About SKN
SKN focus on providing competent technical personnel to carry out solutions from concept to completion in the design, supply, installation, commissioning, maintenance, inspection and integrity assurance of electrical and instrumentation equipment installations, utilising both standard and rope access techniques for the oil, gas, petrochemical and pharmaceutical industries.
SKN strive to combine highly competent personnel, proven processes and ever-evolving technology, to deliver best industry practices ensuring our services exceed client expectations
Client Contact – Stephen Vanderdeyl | Email – stephen.vanderdeyl@sknelectrical.com
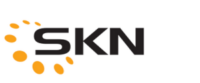
About Inspectivity
At Inspectivity, we’re revolutionising the world of asset management with our cutting-edge digital inspection software. Our platform is a versatile mobile and cloud solution, designed to simplify engineering inspection and asset management, all within a single, user-friendly tool.
Trusted by many tier 1 operators and service providers across a variety of sectors, we’ve harnessed technical expertise and industry-specific workflows to create a digital inspection solution that’s a game-changer.
If you’re ready to take your inspection processes to the next level, we’re ready to provide the ideal solution for you.