Conveyor systems and rotating equipment form the backbone of industrial production across mining, manufacturing, and chemical processing sectors. Yet, they are also among the most hazardous assets on sites, posing risks of entanglement, crushing, and catastrophic mechanical failure. In Australia alone, thousands of conveyors and rotating machines operate daily under conditions that demand rigorous safety and maintenance standards. Failure to adhere can result in injury, downtime, and costly regulatory consequences.
Standards such as AS 4024.3610-2015 and AS 1755-2000 establish the technical baseline for safe design and maintenance of machinery. But compliance alone is not enough. The future lies in digitising inspection and monitoring practices, not just to meet safety thresholds but to drive a culture of continuous assurance.
This article explores how modern digital platforms like Inspectivity are helping industrial operators elevate safety and reliability by digitising two critical areas: Conveyor Guarding inspections and rotating equipment Operator Rounds. Anchored in real-world implementation at a chemical facility, we examine how structured digital inspections deliver traceable data, reduce missed defects, and enable faster interventions.
Conveyor Guarding: The First Line of Defence
Australia’s industrial landscape is laced with an estimated 20,000 to 30,000 conveyor systems, according to a conservative synthesis of data from mining, fertiliser, and general manufacturing sectors (these are anecdotal estimates only). From overland coal conveyors to plant feeders in fertiliser processing, these systems often operate in proximity to workers, creating constant exposure to rotating drums, return rollers, and nip points. In the mining sector alone, ~1,584 sites operate an average of six conveyors each, totalling ~9,500. The pervasive use of conveyors underlines the need for consistent, high-quality guarding inspections.
Why Conveyor Guarding Matters
Conveyor systems are central to bulk material handling in industries like mining, chemicals, and manufacturing.
In high-risk environments like open-cut mines, fertiliser factories, and materials processing plants, conveyors present specific hazards:
- Reach-through incidents where workers attempt to dislodge materials,
- Entanglement with rotating tail pulleys,
- Contact injuries during maintenance when machinery is not fully isolated.
Anecdotal evidence and safety data from Safe Work Australia consistently link guarding failures to severe incidents, including de-gloving, amputations, and fatalities.
Effective guarding prevents access to moving parts, particularly in zones where workers may clear blockages or conduct maintenance. Without it, routine tasks can quickly turn catastrophic.
Australian Regulatory Context
The primary standards governing Conveyor Guarding are:
- AS 1755-2000: Specific to conveyors, it outlines design, operation, and maintenance requirements for safe usage.
- AS 4024.3610-2015: Safety of machinery and general requirements for the design and construction of fixed and movable guards.
These define minimum requirements for guarding layout, material strength, allowable gaps, and access control. Operational sites must not only comply at initial installation but also maintain guarding integrity through routine validation, something many paper-based systems fail to guarantee.
Compliance must be achieved across the entire asset lifecycle: pre-handover (projects) and post-handover (operations). Inspectivity supports both through separate use cases: Compliance Inspections for project sign-off, and Operational Inspections for ongoing assurance.
The Elements of Effective Guarding
An effective guarding program includes:
- Coverage of tail, head, length, hopper, gravity take-up, and access ways.
- Assessment of guarding effectiveness in terms of prevention of reach over, under, through, and around.
- Evaluation of guarding material types (FRP, stainless steel, mild steel) and their degradation/corrosion profile.
Illustrative layout diagrams provide valuable design references. But the key lies in making these inspections consistent, evidence-based, and auditable.
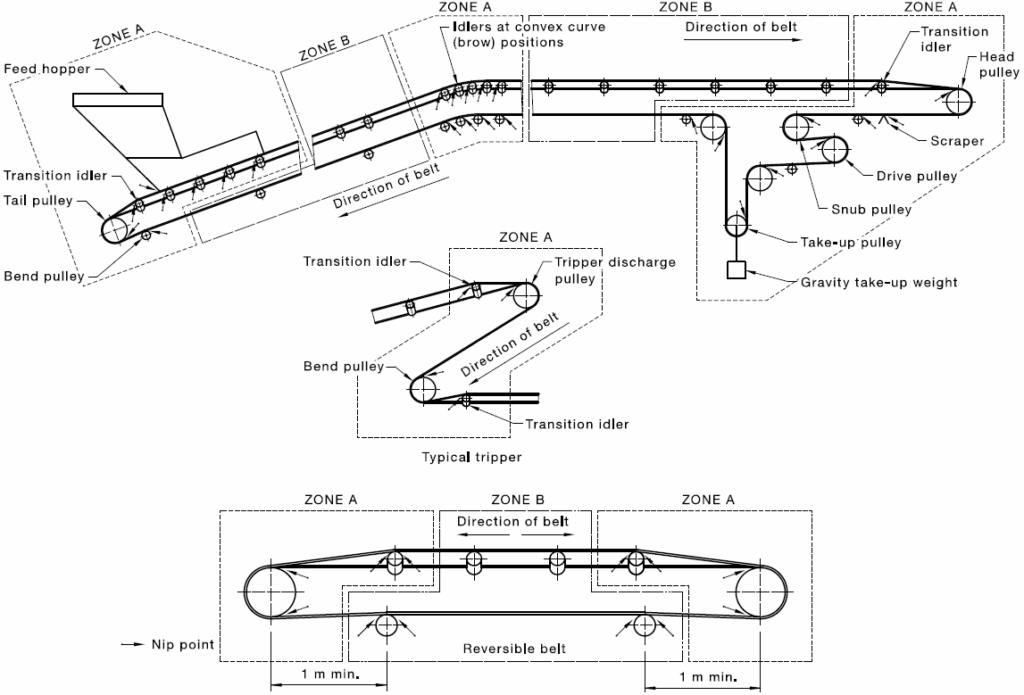
The Cost of Non-Compliance
Failure to meet guarding standards has had devastating consequences:
- In June 2016, a boilermaker at a crushing plant suffered severe injuries when both arms were drawn into the nip point of an unguarded conveyor’s tail-end pulley. The worker attempted to remove a rock from the conveyor without isolating the equipment, leading to de-gloving injuries, friction burns, and multiple fractures. The incident was attributed to the absence of proper guarding and a lack of isolation procedures.
- In February 2020, a worker at a Western Australian mine was fatally injured while cleaning built-up material from underneath an operational conveyor. Despite the presence of guarding, it was insufficient, allowing access to dangerous moving parts. The worker became entangled in the return roller and belt, leading to fatal injuries. The mining company was fined for failing to provide adequate guarding.
- In December 2024, a worker at Clarence Sands Quarry in New South Wales sustained a serious arm injury while adjusting a conveyor belt alignment arm on an unguarded section of a fixed conveyor. His arm became entangled with the belt and rollers, necessitating surgery. The incident highlighted the dangers of working on unguarded machinery and the importance of adhering to safety standards like AS 4024.1.
These are not isolated events. They underscore why guarding inspections should not rely on paper checklists or manual signoffs. Defects like corrosion, missing bolts, or removed panels need photographic evidence, alerting systems, and traceable workflows. These are features embedded in digital platforms like Inspectivity.
Rotating Equipment: Catching Failures Before They Happen
Rotating equipment (e.g., elevators, pumps, agitators, fans, compressors, screens, conveyors, drums) are dynamic assets that wear over time. Operator Rounds, typically performed on a shift basis, serve as frontline condition monitoring. Yet, their effectiveness depends on the structure, consistency, and traceability of the checks performed.
What Are Operator Rounds?
Operator Rounds are routine, structured inspections carried out by operations personnel. Their purpose is to:
- Observe early warning signs of failure,
- Record qualitative and quantitative equipment data,
- Escalate emerging issues before breakdowns occur.
Covered equipment might include:
- Pumps (centrifugal, positive displacement, hydraulic),
- Fans and compressors,
- Screens, elevators, agitators, conveyors, and rotating drums.
What They Look For
Operators check for:
- Auditory signs: unusual noises, whines, knocks,
- Visual signs: oil leaks, vibration, temperature anomalies,
- Functional indicators: auto-lubricator status, pressure readings, gearbox oil levels.
Digital templates, like those in Inspectivity, allow these inputs to be captured with supporting photos and optional alerts. Components such as thrust bearings, gearbox oil filters, and motor assemblies can be assessed for their condition via configurable tabular forms, helping operators note subtleties often lost in free-text paper logs.
Frequency and Best Practice
Rounds are typically scheduled daily or per shift, with frequency adjusted for criticality. While ERP/CMMS systems log history, they rarely surface frontline nuances. Operator Rounds plug this gap, generating actionable intelligence on asset health. Best practices include:
- Use of predefined inspection templates tailored to equipment type,
- Capture of structured data (e.g., motor temp, vibration level),
- Immediate issue escalation via alerts to condition monitoring teams.
This structure enables trending over time, enabling predictive intervention.
Digital Tools for a Safer, Smarter Plant
Limitations of Paper and Spreadsheet-Based Systems
Legacy systems struggle with:
- Missed inspections due to a lack of task visibility,
- Poor traceability of findings and follow-ups,
- No audit trail or image evidence,
- Delayed response to critical issues.
In a high-consequence environment, these gaps are intolerable. Digitisation replaces fragmented records with a single source of truth accessible across Maintenance, HSE, and Operations.
How Inspectivity Supports These Use Cases
Inspectivity’s platform addresses both compliance and condition monitoring needs. Key capabilities include:
- Asset-specific templates:
- Compliance and Operational inspection templates to assess asset health at different points throughout the asset life cycle in Conveyor Guarding.
- Targeted inspection templates for each type of asset (e.g., elevators, pumps, agitators, fans, compressors, screens, conveyors, drums) to capture visual, functional and auditory indicators in Operator Rounds.
- Issue tracking: Defect location, description, risk rating, and associated Work Order info.
- Photo documentation: Required at key checkpoints.
- Alerts:
- Automatic notifications by site or defect type for Conveyor Guarding.
- Operator Rounds trigger defect notifications when condition thresholds are breached.
- RFID support: quick asset ID and reduced error.
All inspections are versioned, timestamped, and include full history. This makes it easier to respond to audits, improve PM schedules, and close feedback loops.
Case Study: A Chemical Company’s Path to Digital Assurance
Background
This Australian chemical company, with facilities spanning several locations, operated over a hundred pieces of rotating equipment and dozens of conveyor lines. Before digitisation, inspections were:
- Recorded on paper,
- Photos lacked important meta-data for context,
- Lacked version control,
- Required manual re-entry to ERP/CMMS.
Supervisors often had little visibility into overdue inspections or defect closeout rates.
Conveyor Guarding Implementation
Using AS 4024.3610 as the standard, the Projects team began with the Conveyor Guarding Compliance Inspection template:
- RFID scan of tail panels,
- Structured questions per conveyor segment (head, length, access way, hopper, etc.),
- Guarding material, reach-over safety, and corrosion condition recorded.
Post-handover, Operations adopted Conveyor Guarding Operational Inspection:
- Verifies guards are intact and unchanged,
- Focus on tail guarding (most common access point),
- Raises alerts if removed, corroded, or blocked.
Supervisors received alerts by site location when issues were found, and all items had defect priority ratings and Work Order links.
Operator Rounds Digitised
Across agitators, fans, compressors, and drums, templates from the Rotating Equipment Checks were rolled out:
- Each inspection captured motor condition, vibration levels, temperature anomalies, and gearbox oil checks.
- Inspection data included structured dropdowns for defect types (e.g., Oil Leak, Auto Lubricator Not Working, etc.).
- Photos and comments were mandatory for defect reports.
- Alerts notified both the condition monitoring engineer and inspection supervisors.
Examples of captured data:
- Agitators: oil level, bearing noise, motor vibration.
- Compressors: temperature, lube oil pump condition.
- Fans: auto-lubricator fluid level, bearing vibration.
- Screens: motor wear and structural noise checks.
Outcomes
- Increased Audit readiness: All inspections traceable, image-backed, and with defect closeout history.
- Increased Data quality: Operators recorded structured data (vs. vague handwritten notes).
- Alerts: 5 operational alerts per site are automated to notify stakeholders, particularly plant supervisors.
This digital transition helped the chemical company eliminate undocumented change, prioritise maintenance, and reduce safety risk exposure.
The biggest win: shift from reactive to proactive maintenance, enabled by structured digital evidence and real-time workflows.
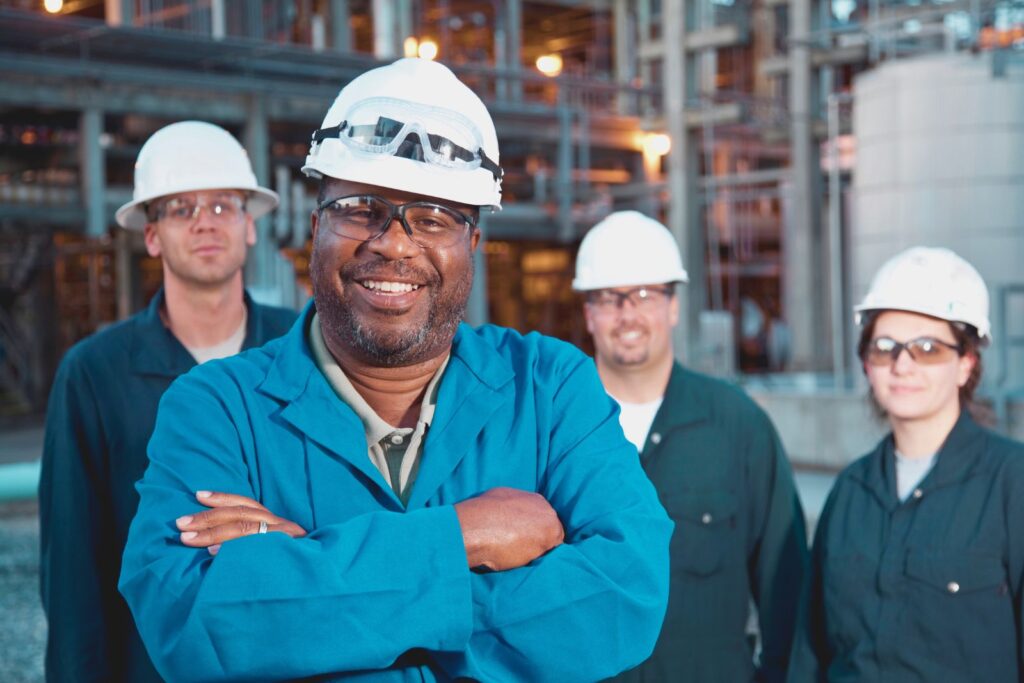
Digital Conveyor Guarding and Operator Rounds Inspections
Conveyor Guarding and Operator Rounds are not just compliance checks, they are risk control measures. When digitised, they become powerful tools for early intervention, maintenance optimisation, and regulatory assurance.
Recommendations for teams starting the journey:
- Start small: pilot Inspectivity on one system or equipment type.
- Configure templates to match your risk profile and asset design.
- Train operators on how to identify and capture useful defect data.
- Use alerts and dashboards to embed insights across teams.
Ultimately, platforms like Inspectivity empower frontline staff to contribute directly to safety and reliability. This ensures compliance isn’t just met, but continuously maintained.
The Inspectivity Platform is purpose-built for seamless Conveyor Guarding and Operator Rounds inspections. Our digital solution offers real-time collaboration, structured data capture, and powerful analytics to standardise workflows, ensure compliance, and enhance worker safety. Ready to move beyond manual methods? Book a software demonstration now to discover how Inspectivity can transform your inspection processes.