The Role of Inspections in Compliance and Safety
In high-risk industries such as energy, resources, oil and gas, and large capital projects, workplace safety is mission-critical. Teams operate in environments where equipment is exposed to harsh conditions, corrosion threats, and significant loads. Consequently, incidents resulting from inadequate maintenance or structural failures can be catastrophic — both from a human safety perspective and from a regulatory standpoint.
Government authorities worldwide have strengthened their focus on corporate accountability, with many jurisdictions introducing industrial manslaughter laws. In scenarios where gross negligence leads to a worker’s death, not just executives and company directors, but also site supervisors and managers can face severe legal consequences. This legislative environment highlights the need for robust compliance strategies, especially around structural access points — ladders, platforms, and handrails — because these are some of the most heavily used yet frequently overlooked assets on-site.
Despite this heightened scrutiny, many organisations still rely on paper-based methods that do not adequately break down the critical aspects of a handrail inspection — such as structural integrity, corrosion, and load-bearing capability — into a clear checklist of items. Additionally, the absence of a standardised asset identification system (e.g., QR codes or RFID tags like EziId) often leads to confusion about which handrail section was inspected or repaired, making it difficult to track issues over time. Photo evidence and other inspection data may be stored arbitrarily on personal devices, jeopardising traceability and leaving safety managers with a fragmented compliance history.
To address these concerns, forward-thinking businesses are embracing digital solutions that unify data capture, documentation, and follow-up in one place. By deploying advanced inspection platforms, teams can systematically tackle each component of a ladder, platform, or handrail — documenting corrosion, verifying load-bearing tests, and logging structural details — all while using RFID or QR-tag scans to ensure accurate identification. Real-time image storage and secure archiving also make it easier to confirm compliance, revisit past inspections, and immediately escalate high-priority repairs, thereby strengthening overall safety protocols and reducing liability.
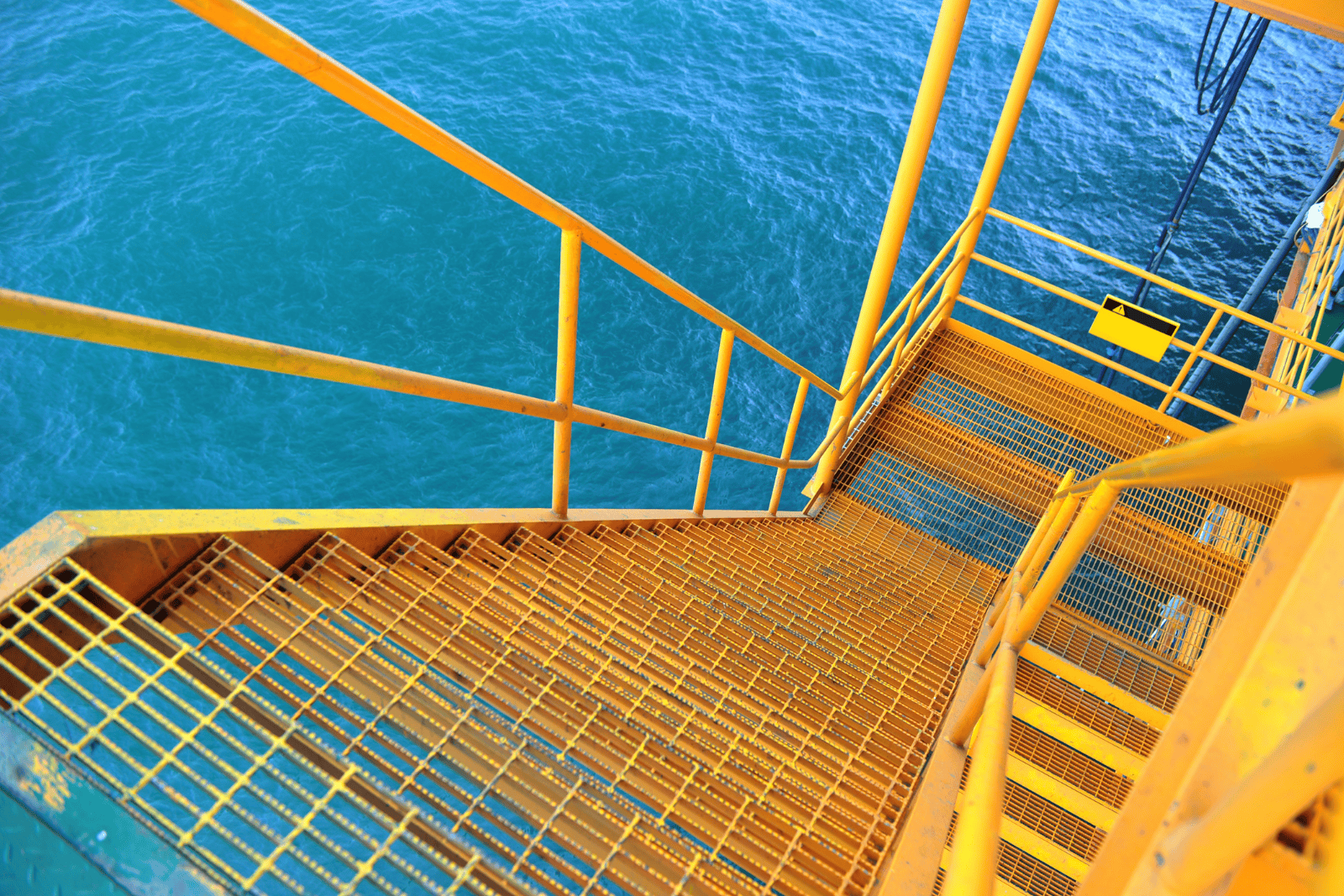
Ladder Inspections: Types, Standards, and Common Issues
Industrial sites typically host a variety of ladders, each designed for specific access requirements. Some facilities rely on fixed vertical ladders with cage enclosures, while others use step-type ladders, twin-stile rung-type ladders, or individual-rung (step-iron) designs. Different ladder architectures introduce different risk profiles. For instance, a caged ladder may mitigate fall hazards but still be prone to corrosion at mounting points if exposed to moisture or chemicals.
Key Challenges and Common Issues
- Corrosion and Wear: In environments with high humidity or chemical exposure, rungs and side rails can corrode or weaken. Inspectors should watch for surface pitting or flaking coatings.
- Loose or Missing Bolts: Fasteners may loosen over time due to vibration or repeated use. Early detection is vital to prevent sudden structural failures.
- Incorrect Pitch or Angle: Safety standards such as AS 1657:2018 specify permissible angles for fixed ladders. Inspectors often use tools like a pitch gauge to verify compliance.
- Inadequate Fall Protection: Some industrial ladders require a self-closing gate, chain, or drop bar at the top. Missing or malfunctioning gates can expose workers to fall hazards.
Relevant Standards and Regulations
In Australia, AS 1657:2018 outlines design and maintenance guidelines for fixed platforms, walkways, stairways, and ladders. Globally, ISO 14122 also stipulates best practices for permanent means of access to machinery. Meanwhile, Workplace Health & Safety (WHS) Regulations across different regions impose strict obligations on employers to ensure ladder stability and worker safety. By adhering to these standards, organisations reduce the likelihood of legal repercussions and create safer worksites.
Platform Inspections: Structural Integrity and Safety
Platforms are essential in industrial operations, granting maintenance crews and operators a stable working surface for tasks performed at height or around machinery. A single platform collapse can halt production, compromise worker safety, and expose the organisation to liability. Regular platform inspections are, therefore, imperative.
Core Areas of Focus
- Structural Stability: Inspectors must confirm that the platform can handle the required loads without deforming. Frame members, beams, and support brackets should show no evidence of fatigue or cracks.
- Guardrailing and Toeboards: Platforms typically require railings around edges and toeboards at the perimeter to protect against falls and dropping objects. Missing or damaged toeboards, for instance, can lead to tools falling onto work areas below.
- Slip Resistance: In the energy and resources sectors, oils, chemicals, or water can accumulate, creating slip hazards. Inspectors should verify that flooring surfaces have adequate traction, whether through grating, anti-slip coatings, or raised cleats.
- Edge Protection: Some platforms may have vulnerable edges where equipment is loaded or removed. Additional protective measures, like removable railing sections or self-closing gates, can mitigate risks.
Compliance Context
AS 1657:2018 specifies design loads and mandates certain dimensions for platforms, ensuring enough surface width, enough head clearance, and strong guardrails. ISO 14122-2 extends these guidelines to platforms and walkways in machinery environments. Companies must also factor in local WHS requirements that emphasise robust fall prevention and safe access. Failure to comply can have serious operational and legal ramifications.
Frequent Issues
Worn surfaces, rust on critical joints, and unapproved modifications to platform designs (such as cutting into structural beams for custom fittings) often arise in audits. Addressing these issues proactively not only satisfies compliance but also prevents expensive unplanned shutdowns.
Handrail Inspections: Safety, Load Testing, and Compliance
Handrails are integral to worker well-being, particularly in areas where employees move across elevated pathways or around rotating equipment. They provide a primary line of protection against falls. An effective handrail system typically comprises rails, stanchions, welds, mounts, and sometimes, kick rails or infill panels for added security.
Load Testing and Structural Integrity
Standards like AS 1657:2018 outline minimum load requirements for handrails, ensuring they can handle a lateral load from a person leaning or a sudden impact. Hammer Tests or deflection tests are commonly used to measure the rail’s response to force. If a handrail deflects significantly under normal loads, it should be flagged for reinforcement or replacement.
Guardrails vs. Rigid Rail Systems
While “guardrail system” is a broad term for passive protection around open edges, a “rigid rail system” often refers to an overhead track used with personal fall-arrest gear. The two are not identical: guardrails aim to prevent individuals from reaching a drop-off whereas rigid rails serve as an anchor for harnesses. Many facilities employ both approaches — guardrails to passively protect edges and rigid rails to safeguard workers in specialised tasks like overhead crane maintenance.
Typical Compliance Drivers
- AS 1657:2018 details handrail and guardrail design, highlighting required heights and infill spacing.
- ISO 14122-3 specifies permanent means of access for industrial machinery, emphasising robust handrail construction.
- OSHA 1910.29 in the United States provides guidelines for fall protection systems, ensuring surfaces are guarded by rails of a prescribed height.
Regular inspection programs check for corrosion at mounts, cracks in welds, and signs of mechanical damage from forklift impacts or other collisions.
The Benefits of Digital Inspection Systems
In an environment where even minor oversights can result in severe accidents, digital inspection systems offer a transformative leap in risk management and operational efficiency. While the foremost benefit is enhanced safety for the workforce, organisations also gain better compliance and stronger asset management capabilities.
Reduced Risk Through Standardisation
Digital platforms replace inconsistent paper-based checklists with standardised templates, leaving less room for human error. By building templates around recognised guidelines — such as AS 1657:2018 — inspectors can systematically verify each step required for compliance. Errors or omissions become far less likely because the system enforces logical sequences and mandated photographs.
Real-Time Insights and Rapid Response
A digital workflow provides immediate visibility into open issues. Supervisors can track which inspections found critical defects and quickly schedule repairs. Photo or video evidence aids in deciding if an immediate shutdown is warranted or if the matter can await scheduled maintenance. This near-instant escalation mechanism can be vital in preventing accidents or halting further damage.
Automation and Audit Trails
By logging each inspection event, digital systems maintain a time-stamped trail that can be invaluable for audits or regulatory inquiries. When legal or compliance teams request proof of inspection frequency, the organisation can produce comprehensive records at the click of a button. This process can be crucial in an era of industrial manslaughter laws, where an inability to demonstrate due diligence could lead to severe consequences.
Workflow Integrations
Digital inspection tools often integrate seamlessly with enterprise resource planning (ERP) systems, computerised maintenance management systems (CMMS), or project management software. As soon as a defect is identified, an automated ticket can be created in the maintenance backlog, eliminating communication gaps and speeding up resolution times. Over the long term, this fosters a culture of continuous improvement and proactive risk reduction.
Elevated Safety Culture
By making it easier for workers to flag issues and share insights, digital solutions encourage a more open conversation around safety. Capturing images on-site with a mobile device or scanning an RFID tag to confirm the exact handrail or ladder in question not only simplifies the inspection process but also empowers workers to contribute meaningfully. Their involvement in a streamlined system fosters accountability and a heightened sense of ownership.
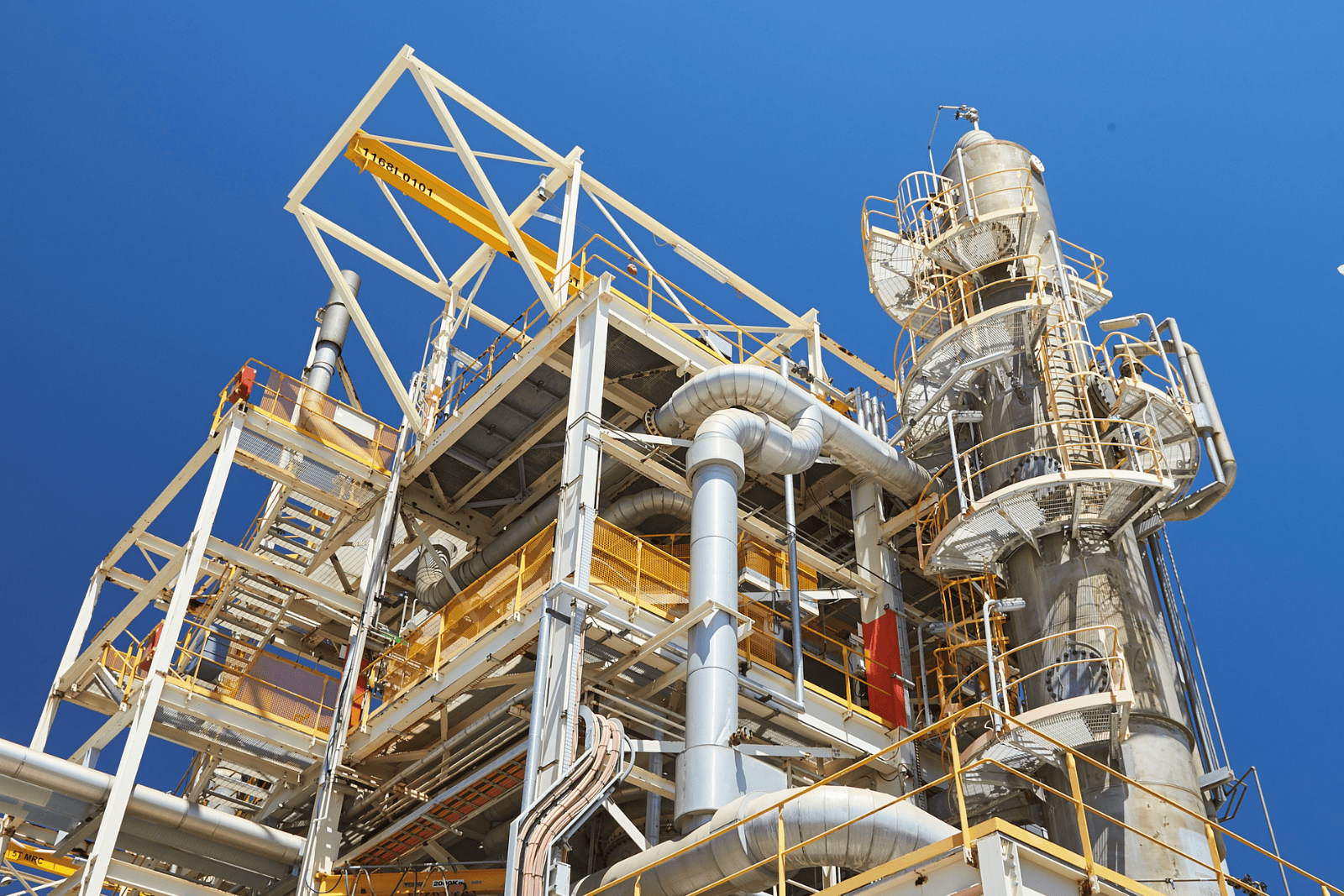
Take Your Inspections to the Next Level with Inspectivity
When it comes to ladder, platform, and handrail inspections, Inspectivity offers a modern approach that merges best practices with advanced technology. Built to support industries where safety is paramount, Inspectivity’s digital platform tackles the core challenges that organisations face daily — compliance, traceability, and efficient workflow management.
Key Features
- Customisable Templates: Align your inspection forms directly with AS 1657:2018 or any relevant global standard. This ensures consistent processes across all sites, regardless of local variations.
- Mobile-Enabled Data Capture: Inspectors can complete checklists on mobile devices, attach photos or videos, and log real-time comments. Scanning a QR code or RFID tag verifies which asset is under review, reducing identification errors.
- Automated Reporting: With automated metrics and dashboards, managers gain immediate insights into inspection outcomes, open defects, and resolution progress. Such transparency helps maintain a proactive stance on safety.
- Integration with Asset Management: Inspectivity integrates seamlessly with maintenance and enterprise systems, so identified issues can be escalated to maintenance teams with minimal friction. This reduces administrative overhead and ensures timely interventions.
Real-World Success Stories
Two examples illustrate how Inspectivity drives tangible safety and efficiency outcomes:
Wesfarmers Chemicals, Energy & Fertilisers
Wesfarmers Chemicals, Energy & Fertilisers (WesCEF) operates a diverse portfolio of chemical, energy, and fertiliser businesses across Australia. Within WesCEF, CSBP Fertilisers play a key role in manufacturing and distributing fertilisers that support both local and international agriculture.
Ongoing Handrail Inspection Campaigns at CSBP Fertilisers
Over several years, CSBP Fertilisers has run multiple handrail inspection campaigns to enhance safety and compliance across its facilities. Leveraging the Inspectivity Platform, these campaigns have resulted in:
- 7,931 inspections conducted
- 59,434 photographs captured for comprehensive documentation
- 12,481 issues identified and managed
By digitising their inspection processes, CSBP Fertilisers has significantly improved compliance tracking, reduced administrative overhead, and enhanced operational oversight. For more details, refer to the WesCEF case study on Inspectivity’s website.
Workplace Access & Safety
Workplace Access & Safety (WAS) is a leading Australian company specialising in height safety engineering. They offer comprehensive services, including risk assessments, inspections, testing, installation, and training, to help workplaces comply with working-at-heights legislation and prevent fall-related incidents.
Ladder and Platform Inspection Initiatives
Over the years, WAS has undertaken extensive ladder and platform inspection projects to enhance safety and compliance across various facilities. Utilising the Inspectivity Platform, these initiatives have encompassed over 200 projects, resulting in:
- 25,267 inspections conducted
- 79,917 photographs captured for detailed documentation
- 11,331 issues identified and managed
By digitising its inspection processes, WAS has improved the consistency and speed of assessments, enabling clients to address safety concerns proactively. For more details, refer to the WAS case study on Inspectivity’s website.
Digital Handrail, Ladder and Platform Inspections
The Inspectivity Platform is purpose-built for seamless ladder, platform, and handrail inspections. Our digital solution offers real-time collaboration, structured data capture, and powerful analytics to standardise workflows, ensure compliance, and enhance worker safety. Ready to move beyond manual methods? Book a software demonstration now to discover how Inspectivity can transform your inspection processes.