Operations Management Systems for Petrochemicals
The petrochemical industry is one of the most complex operational environments, where efficiency, safety, and regulatory compliance go hand in hand. Yet, many operational teams today grapple with challenges that outdated systems cannot overcome. While effective for managing financials and supply chains, reliance on ERP systems becomes a significant hurdle when managing detailed technical data, real-time problem resolution, and field-level collaboration. The limitations in these traditional systems create headaches for operations and engineering teams, resulting in inefficiencies and sleepless nights for those responsible for ensuring safety and compliance.
The Challenge
The Struggle with Technical Data Storage
Imagine an engineering team that needs somewhere to store crucial technical data about the assets they manage. They attempt to use their ERP system, but it’s not designed for this depth of technical detail. The outcome? Technical information ends up in PDF Maintenance Data Records (MDRs), scattered across a maze of file systems that no one can easily navigate. When field inspectors need to validate conditions using OEM certification documents, they simply can’t get to them fast enough. Important documentation is locked away, often several clicks too deep in an obscure folder, making it practically impossible for the field team to assess any special conditions in real time.
Inefficiencies in Inspection History Management
The inspection history is no better. Despite the critical nature of inspections, many teams still rely on Excel spreadsheets to track their inspection data. These spreadsheets lack standardisation, transparency, and security. Imagine an offshore engineer trying to demonstrate compliance during an audit – only to realise the records they need are hidden among dozens of spreadsheets and disparate files. The fear of not being able to prove compliance is real and keeps many operations leaders up at night, especially when a regulatory audit is just around the corner, threatening a potential stop notice that could cripple operations.
Challenges in Offshore and Onshore Collaboration
Then there’s the issue of collaboration between offshore and onshore teams. When an inspector finds a problem in the field, they should be able to scope it immediately and initiate corrective actions. However, the ERP system isn’t designed for real-time collaboration or seamless issue scoping. Instead, the discovery of issues often happens in isolation – the details are recorded, perhaps even inconsistently, and then passed on days later, delaying any chance of team collaboration or starting a corrective action promptly. The result is often poorly defined issues, unclear communication between teams, and a lag between discovering a problem and addressing it. There is no real-time connection between teams to address these problems effectively.
Lack of Consistency in Inspections
Another challenge is the lack of visibility and consistency in how inspections are performed. Different inspectors have different approaches, and there is no standard format. Photos are often missing, leaving no visual record of asset condition. How do we even know whether inspections were properly carried out in the field, or just rubber-stamped back at the desk?
The lack of consistency and transparency not only affects quality but also undermines the trust that should exist between different stakeholders – from management to field inspectors and of course with the regulator.
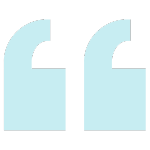
25% of our instruments were calibrated perfectly to two decimal places. Are we that perfect or is the work being completed at the desk?
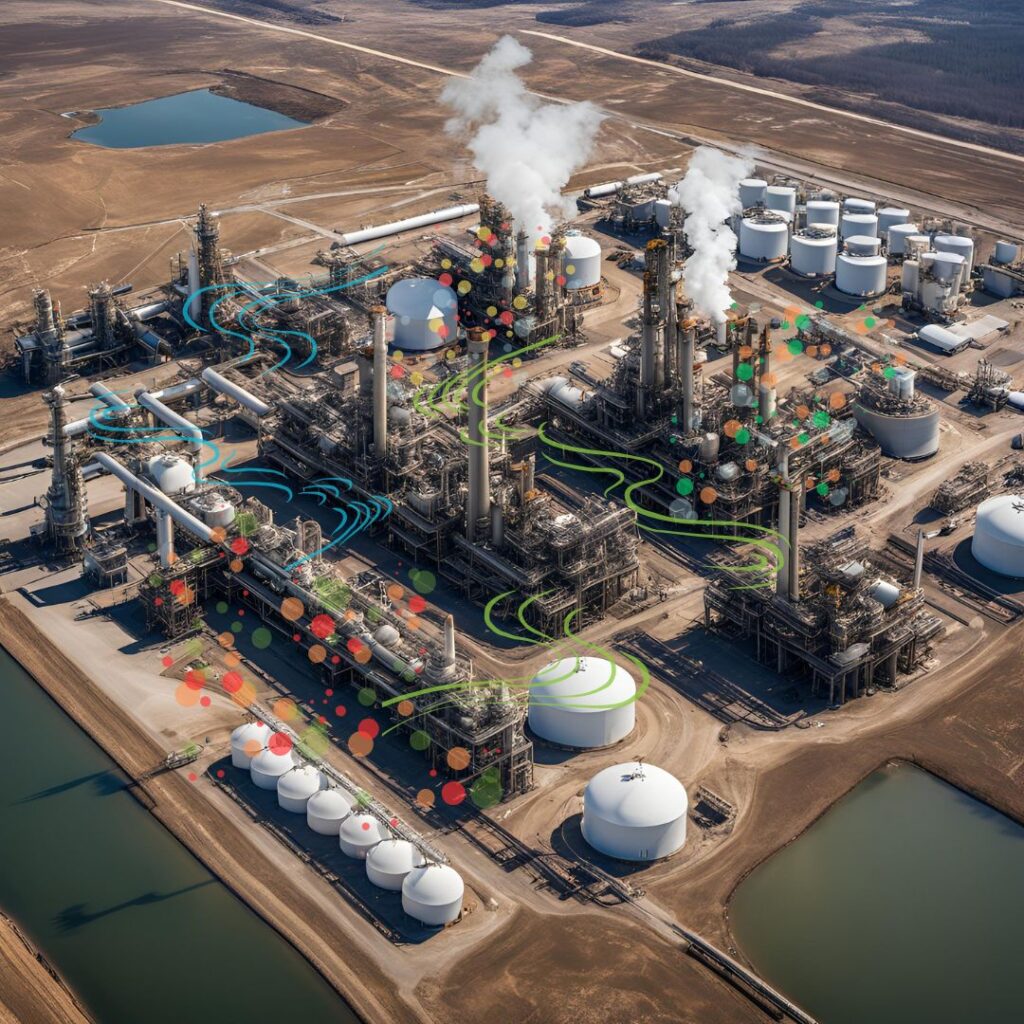
A Wide Variety of Inspections
The variety of inspections required in petrochemical operations is staggering – compliance inspections, asset integrity checks, coating and fabric maintenance, flange management, inspections of portable and third-party equipment, lighting surveys, fire and gas system checks, cable tray inspections, and much more. Each of these inspections comes with its own set of requirements and intricacies. Managing these diverse inspections using outdated systems creates a chaotic and inefficient process, leading to inconsistencies and potential safety risks.
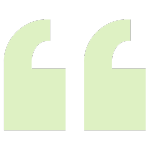
Technologies like AI and predictive analytics are out of reach for many petrochemical companies simply because their data isn’t digital, accessible, or in a form that these technologies can use.
Barriers to Technology
Moreover, modern technologies like AI and predictive analytics are out of reach for many petrochemical companies simply because their data isn’t digital, accessible, or in a form that these technologies can use. Inspection data, maintenance records, and asset information are often fragmented and stored in formats that AI can’t work with. When data is scattered across spreadsheets, PDFs, and paper records, the promise of AI-driven insights remains an unfulfilled potential, further compounding inefficiencies.
Preparing for AI adoption in operations management involves understanding and organising your company’s engineering and asset data estate. This foundation is critical for effective AI workflows and allows companies to harness advanced tools, such as domain-specific AI solutions. As AI becomes integral to enterprise operations, energy companies must prioritise data readiness to unlock AI’s full potential and secure a competitive edge in the evolving market.
The Status Quo
In short, a typical petrochemical operations team can find itself with the following struggles:
- Fragmented data storage: Technical details in inaccessible PDFs, OEM certifications hard to retrieve, and inspection histories locked in inconsistent spreadsheets.
- No real-time collaboration: Issues are identified without proper scoping, delaying corrective actions, and limiting offshore-onshore cooperation.
- Lack of consistency in inspections: Different inspection methods, missing photos, and no real standardisation lead to unreliable inspection records.
- High variety of inspection types: Numerous specialised inspections are difficult to manage cohesively, increasing risks and inefficiencies.
- Limited access to modern tech: AI and analytics are not feasible because data is missing, incomplete, or not in a usable format.
A Comprehensive Solution
These problems represent the status quo for many petrochemical companies today. It’s a situation that demands a comprehensive solution – a system that goes beyond the limitations of an ERP, providing a robust, asset-centric platform that can centralise technical data, enable real-time collaboration, and ensure that every inspection is standardised, documented, and accessible. This is where a dedicated Operations Management System (OMS) like Inspectivity comes into play, providing a single, integrated platform designed specifically to address the unique challenges of complex, multidisciplinary petrochemical operations.
Leveraging an Operations Management System (OMS) will improve operational efficiency, safety, and compliance by centralising data, automating processes, and facilitating real-time decision-making. In the context of the petrochemical industry, one of the core focuses of an OMS is Barrier Management – a systematic approach to identifying, maintaining, and assessing the performance of barriers that are put in place to prevent incidents or mitigate their consequences.
Barrier Management is a fundamental aspect of operational safety. As discussed in a DNV article on Barrier Management, safety barriers are the means through which risks are managed proactively, ensuring that undesirable events are either prevented or their impact minimised. A well-implemented OMS provides the structure needed to effectively monitor these barriers, ensuring they remain robust and effective throughout the asset lifecycle.
Barriers can be technical, such as firewalls or emergency shutdown systems; operational, such as protocols for inspections; or organisational, involving the coordination and training of personnel. The Principles for Barrier Management outlined by the Petroleum Safety Authority (PSA) Norway stresses that barrier management is not a one-off task but a continuous process of assessment, monitoring, and improvement. This ensures that the systems and processes put in place to manage risks are not only effective at the outset but remain so throughout the life of the asset.
How Barrier Management Integrates with an OMS
An OMS like Inspectivity provides a comprehensive platform for managing inspections, tracking asset conditions, and maintaining an accessible history of defects and actions taken. Barrier Management can be integrated into Inspectivity by using its powerful inspection management tools to ensure that all safety barriers – whether technical, operational, or organisational – are routinely inspected, maintained, and tracked. This includes setting up custom inspection templates for barrier assessments, capturing data on barrier performance, and using the platform’s risk calculation tools to determine the effectiveness of each barrier. By centralising barrier-related inspection data, Inspectivity ensures that safety barriers are consistently monitored, allowing teams to identify weaknesses and take timely action to maintain their integrity. The platform also supports effective communication between teams, ensuring that any issues with barriers are promptly addressed and resolved, contributing to ongoing operational safety and regulatory compliance.
Key Questions for Barrier Management in OMS
To ensure effective Barrier Management, an OMS needs to address several key questions:
- What are the major risks that could lead to potential incidents?
- What are the critical barriers we rely on to control those risks?
- What minimum level of performance do the critical barriers need to deliver?
- How do we ensure the critical barriers are effective throughout the lifecycle of the asset?
By answering these questions, an OMS helps petrochemical companies transition from a reactive stance to a proactive risk management approach. This shift not only ensures compliance with tightening regulations but also builds resilience within operations, helping to prevent major incidents before they occur.
Barrier Management in Practice: Enhancing Safety and Compliance
Effective barrier management leads to ongoing safety management by focusing on the prevention and mitigation of major hazards. This is critical in ensuring that operations in environments like the petrochemical sector are conducted with the highest possible safety standards. The integration of OMS with comprehensive barrier management tools allows teams to move beyond paper-based processes, ensuring that all critical information – such as inspection records, barrier statuses, and risk assessments – is easily accessible and actionable.
By leveraging real-time data, Inspectivity ensures that every inspection, assessment, and corrective action feeds directly back into the system, maintaining up-to-date risk data. This transparency is crucial for demonstrating regulatory compliance and for providing peace of mind to operational teams, knowing that every possible measure is being taken to prevent incidents.
Ready to take your barrier management to the next level?
Whether you’re the technical authority, supervisor or inspector, ensuring the safety of your operations is paramount. By adopting a digital inspection platform like Inspectivity, you can streamline your compliance processes, reduce time spent on inspections, and ensure that your operations management systems meet the highest standards.
Don’t wait – take action now to enhance your compliance and safety performance. Contact us today to learn how Inspectivity can revolutionise the technical systems that back up your teams.