The Hidden Costs
Enterprise Resource Planning (ERP) systems and Computerised Maintenance Management Systems (CMMS) like SAP, Oracle, or Microsoft Dynamics 365 have become integral to managing finances, supply chains, and high-level maintenance schedules in many asset-intensive industries. Yet, while these platforms excel in accounting and overarching resource planning, they often fall short in addressing real-time, field-based operational needs — especially when it comes to complex inspection activities.
When companies rely heavily on a one-size-fits-all ERP or CMMS platform to manage day-to-day field operations, the initial promise of “single-system efficiency” rapidly morphs into a maze of inefficiencies. ERP implementation teams may overlook key business requirements, leading to rigid customisations. The result? Limited support for detailed technical data, slow paper-based workflows, challenges in capturing visual evidence, and a poor flow of critical information between onshore offices and offshore sites. This disconnect undermines not just operational efficiency, but also compliance, data integrity, and future scalability.
Moreover, engineering teams — who require precise, asset-level data — find that typical ERP/CMMS fields often cannot capture the variety of information needed for thorough inspections. These limitations emerge in issues as simple as restricted field lengths to manage asset data, or the near-impossibility of embedding images and videos in the system. Realistically, these shortfalls force many organisations back to paper, PDF forms, or Excel sheets to fill in the gaps. This article explores how such a heavy dependency on ERP/CMMS can hamper operational excellence and highlights why a more specialised, digitised approach offers a superior path forward.
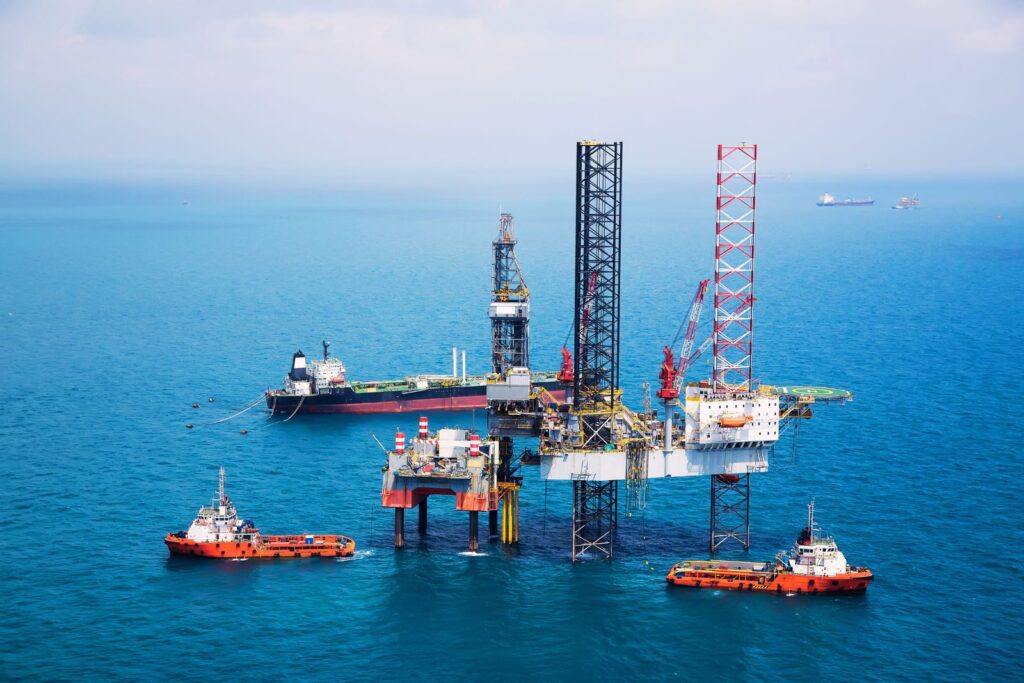
What are the Limitations?
Not the Correct Technology
ERP & CMMS cannot store the variety of operational data required
Many organisations discover too late that the fields in their ERP or CMMS are simply not designed for the depth and breadth of data needed during asset inspections. For example, certain systems limit fields to only 20 characters — an arbitrary yet crippling constraint for technicians trying to capture nuanced details. Because the maintenance team’s requirements are rarely explored during initial implementation, these systems end up with truncated data fields, forcing critical information into PDFs, emails, or external databases. When that data inevitably goes stale or remains inaccessible, risk management and maintenance planning both take a hit.
No visual record: No support for images or video
Inspection workflows often hinge on visual evidence: photographs to aid location of the equipment or track corrosion, videos to confirm vibration, or annotated images to document defect conditions. Traditional ERP/CMMS systems generally handle text-based data well but rarely accommodate large volumes of pictures or video logs.
Without visual documentation:
- Identification of specific faults becomes a guessing game.
- Condition trend analysis over time lacks clarity.
- Audit & trust degrade because top management cannot easily verify on-the-ground repairs.
- AI & Machine Learning initiatives stall — visual data is a treasure trove for advanced analytics.
ERP and CMMS Mobile solutions are expensive and inflexible
This is one of the most significant pain points that arises when organisations try to mobilise their ERP or CMMS. Adding or customising mobile modules for real-time data entry often demands extensive (and expensive) professional services. In many cases, the user interface is counterintuitive, offline functionality is weak, and licensing can climb into the six-figure range.
Let’s look at the challenges of using SAP Mobile system for inspection workflow management. Achieving complete inspection functionality through SAP typically requires multiple modules such as SAP Enterprise Asset Management (SAP EAM), SAP Quality Management (SAP QM), and SAP Asset Manager. Each step involves custom development, costly cloud services (SAP Business Technology Platform, SAP Mobile Start), and at least a year of fine-tuning. During that time, users often juggle multiple apps with inconsistent user interfaces. Rather than a unified approach, teams battle with siloed data and duplicated processes.
Inefficient Processes
Paper-based workflows lead to double handling and inefficiency
Because ERP/CMMS technology does not easily adapt to real-world inspection needs, teams frequently revert to paper forms or spreadsheets. Data is then manually re-entered into a central system — if it is re-entered at all. This process doubles the administrative load, introduces transcription errors, and slows decision-making. By contrast, modern digital inspection systems can save 30-50% of man-hours by automating these manual tasks.
Disconnect between CMMS and fieldwork status
A significant operational gap appears when offshore teams complete inspections but can’t update the CMMS in real time. Delays in data entry compound over days or weeks, resulting in mismatched schedules, rework, or redundant checks.
For example, a common scenario for Offshore drilling contractors is the repeat of compliance tasks simply because the CMMS is not “aware” of previous certifications. They do not maintain their inspection reports to their advantage:
- Scenario 1: Oil Company A contracts Drilling Company B at Location M. Drilling Company B hires Inspection Company C to perform Electrical Equipment in Hazardous Areas (EEHA) inspections on its drilling rig. If the work is performed to an international standard, this certification will be valid for several years, however in some cases this compliance is not synchronised to the CMMS.
- Scenario 2 (Six Months Later): Oil Company X hires Drilling Company B for a new project at Location N. Drilling Company B’s CMMS is not “aware” of the previous certification so they commission another EEHA certification. Wasting time, costs, and impacting efficiency.
- The root cause: The CMMS never centralised or tracked the previous EEHA reports. Onshore teams had no visibility of recent inspections, exposing a major data gap that a modern digital platform would have prevented.
Poor collaboration between onshore and offshore teams
Without robust collaboration tools built into the maintenance workflow, offshore teams operate in isolation until they physically (or manually) transmit results onshore — often days or weeks later. By then, management and engineering staff struggle to rectify issues proactively. When the stakes involve asset integrity or safety compliance, the cost of delayed collaboration is steep.
Poor visibility of results.
The limitations around data capture, combined with a lack of real-time collaboration, make results opaque. Critical insights — like whether an issue was marked urgent or has regulatory implications — can remain hidden until forms are processed. This lags critical decisions, preventing a move from reactive to proactive maintenance strategies.
Poor Culture
Trust issues: Is the data accurate?
When leadership sees suspiciously repetitive results — say, 25% of instrument calibrations returning “perfect” readings year after year — doubt forms about the integrity of reporting. Without verifiable digital evidence (like date-stamped images or sensor data), management cannot confirm whether the technician truly conducted the checks on-site or simply filled in placeholders at a desk.
Standards are not documented (tribal knowledge is lost)
Senior engineers and inspectors carry decades of domain expertise in their heads, but that knowledge rarely gets transferred systematically. When these veterans retire or move on, the organisation loses critical institutional memory. Without structured documentation of best practices, teams end up improvising, leading to divergent methods across different sites or disciplines.
Inconsistent and poorly documented results
One location might track insulation thickness in millimetres, another in inches, and a third site might skip that measurement altogether. Without a unified, digitised standard for each asset type, organisations lose the ability to benchmark or comply with audits systematically. Regulatory compliance and standards often demand uniform reporting; failing to meet these requirements can invite penalties or reputational harm.
Poor Data Quality
Not audit-ready: Regulator concerns & industrial manslaughter risks
In high-risk sectors, incomplete inspection data is more than just an administrative oversight — it poses legal exposure. In some jurisdictions, laws addressing industrial manslaughter make companies and individuals (directors, managers, supervisors) liable if poor maintenance data directly contributes to a fatal incident. Auditors will look for consistent, trustworthy records. Missing or outdated files raise immediate flags about compliance culture.
The inability to drive engineering outcomes
Shortfalls in data quality hamper every stage of engineering and maintenance. When risk-based inspection planning or reliability-centred maintenance strategies rely on incomplete data, the resulting predictions can be misleading or outright wrong. This leads to either over-servicing (wasting time and money) or under-servicing (jeopardising safety and reliability).
Failing to unlock the future of operations due to poor data
Modern asset management techniques revolve around advanced analytics, Machine Learning (ML), and AI-driven tools. These technologies hinge on:
- Large Language Models (LLMs) – Need structured, context-rich data to provide meaningful insights.
- Scalable infrastructure – Siloed or messy data is difficult to integrate into enterprise analytics.
- Prompt engineering – AI queries require consistent, well-labelled data for optimum results.
- Guardrails & security – Data governance is challenging if your data is unverified or scattered.
- High-quality data – Possibly the biggest barrier to AI adoption in industrial settings.
Companies that fail to digitise effectively will likely find themselves outperformed by competitors who use high-quality data to refine everything from maintenance schedules to capital investment decisions.
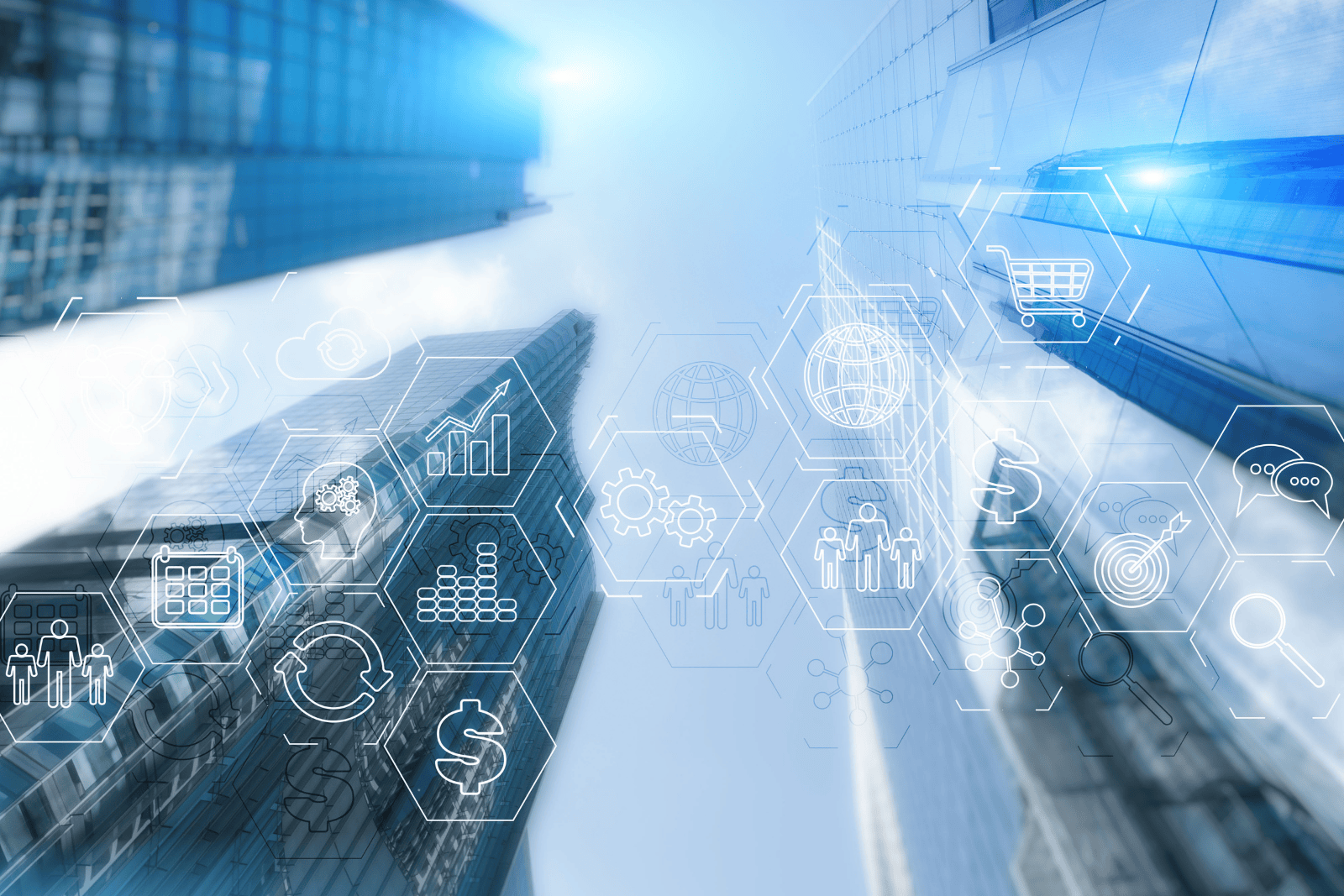
The Benefits of a Digitised Asset Inspection Management System
A modern, purpose-built digital inspection platform stands apart from traditional ERP/CMMS by being more agile, real-time, and data-rich. Here are the key advantages:
Digital Inspections Address the Gaps in ERP & CMMS
- Seamless data capture: Instead of cramming details into limited CMMS fields, a specialised system allows for detailed static technical data, comprehensive use case-specific forms and key documentation.
- Real-time updates: Free from reliance on PDFs and Excel spreadsheets, the data flows instantly between the field and the office.
- Verified records: Photographs, videos, and inspection data build transparency and trust.
- AI-readiness: Data is stored in a structured format from the get-go, priming organisations for advanced analytics down the road.
Improved Collaboration & Operational Efficiency
- Real-time updates for compliance: Technicians in the field can instantly mark an inspection as completed, attaching photos to prove compliance.
- Onshore-offshore synergy: Teams align on the same data, enabling near-instant feedback on issues or anomalies.
- Reduced redundant work: Historical records are easy to locate, preventing repeated inspections just because data was misplaced or the system never updated.
AI-Powered Decision-Making & Predictive Maintenance
- Early anomaly detection: With consistent data capture, AI algorithms can spot warning trends before they become crises.
- Smarter asset lifecycle management: Predictive maintenance strategies– fuelled by robust data — reduce downtime and extend equipment lifespans.
Quantifiable ROI: Over time, the predictive insights generated can help rationalise maintenance budgets, steering resources precisely where they are needed most.
How Inspectivity Bridges the Gap
Inspectivity is designed from the ground up to handle the complexities of asset inspections and operational management:
- Purpose-built digital inspection platform: Unlike generalist ERP modules, Inspectivity focuses on field inspections and compliance tasks — ensuring it supports the full range of operational data, from numeric forms to visual records.
- Fully integrated yet independent of ERP limitations: You can complement your existing ERP, preserving the financial and scheduling strengths of your enterprise systems while offloading field data collection to a platform that excels in capturing inspection detail.
- Enables real-time, structured, and AI-ready data collection: Every inspection record is consistently stored and easily retrievable, eliminating the guesswork caused by siloed PDFs or half-filled spreadsheets.
- Trusted by industry leaders: Companies in petrochemical, mining, and energy sectors have turned to Inspectivity for improved reliability, compliance, and cost savings. Their ability to unify onshore-offshore data has reportedly cut inspection man-hours by up to 50%.
By integrating seamlessly with your core systems, Inspectivity removes the friction that so often slows ERP/CMMS deployments. Field personnel gain a single, intuitive interface for day-to-day inspections, while managers and engineers can see the big picture via real-time dashboards. Critical issues surface immediately so that the right people can take the right actions without delay.
Call to Action
Are you still relying on aging ERP/CMMS systems to manage the intricacies of asset inspections? It may be time to rethink your operational strategy. The stakes — including safety, compliance, and cost — are too high to ignore. By implementing a specialised, digital inspection management platform, your organisation can move beyond the fundamental weaknesses inherent in a one-size-fits-all approach and embrace modern, AI-ready data strategies.
Discover how the Inspectivity Platform can modernise your inspections. Our digital inspection solution integrates seamlessly with existing ERP systems, providing a powerful, user-friendly interface for both onshore and offshore teams. See for yourself how real-time collaboration and structured data capture can slash costs, enhance safety, and drive operational excellence.
Book a demo today to take the first step toward efficient asset management. The future of reliable, data-driven inspections is closer than you think. Our team is ready to show you how easy it is to adopt a platform built for modern operational challenges, leaving behind the limitations and inefficiencies of an overburdened ERP/CMMS.