Managing operations activities across industrial assets is a complex challenge, requiring strict adherence to diverse regulatory frameworks spanning a range of domains such as electrical, mechanical, and structural. Compliance is a moving target, as evolving standards demand continuous updates to inspection protocols. Beyond regulations, inspections involve specialised technical knowledge — whether it’s ensuring high-voltage equipment integrity, calibrating instrumentation, or conducting non-destructive testing. Asset lifecycle management further complicates the process, as inspections must track equipment from commissioning to operation and decommissioning, maintaining a centralised and consistent historical record.
Compounding these challenges, inspections often occur in harsh environments, from offshore platforms to high-risk electrical zones, demanding robust tools and expert personnel. Data standardisation across these varied inspections is crucial for maintaining accuracy, ensuring seamless integration with maintenance and enterprise systems. Below is an example of the complexity asset owners face in capturing and managing maintenance data, highlighting the breadth of use cases that require structured, reliable inspection workflows.
Compliance Use Cases
Electrical Equipment in Hazardous Areas (EEHA)
Ensuring compliance with EEHA standards involves verifying that all electrical equipment (fixed and portable) in hazardous areas is properly rated and installed. It reduces the risk of ignition sources and ensures ongoing safety in potentially explosive environments. It requires adherence to standards such as IEC 60079.
Potential Dropped Objects
Teams review and document any items or fixtures that could become unsecured and fall from elevated areas, posing risks to personnel and operations. They ensure compliance with safety regulations by systematically identifying these hazards and implementing measures to prevent dropped objects.
Electrical and Instrumentation (E&I) Use Cases
Instrument Calibration
Electrical and Instrumentation (E&I) calibrations involve adjusting and verifying measuring devices to ensure they produce accurate readings within specified tolerances. This process is crucial for maintaining consistent performance and compliance with safety or quality standards.
Motors
This use case covers the inspection and maintenance checks required to confirm motor reliability and operational efficiency. It focuses on testing electrical connections, insulation, and mechanical components to detect issues early and ensure consistent performance.
Cable Tests
Involves verifying the integrity, continuity, and insulation of installed cables in electrical and instrumentation systems. The tests confirm that the cables meet required safety and performance standards, preventing electrical failures or potential hazards.
High Voltage (HV) Equipment
Inspections and maintenance activities for high-voltage electrical and instrumentation systems. It focuses on ensuring the safe and reliable operation of power distribution, control, and protective devices within industrial environments.
Operator rounds
Operator rounds are routine inspections where field personnel walk through designated areas to check equipment status and record operational data. They help identify potential issues early, ensuring equipment remains safe, reliable, and compliant with required standards. Often targeted to E&I equipment but many other equipment categories also (such as rotating equipment).
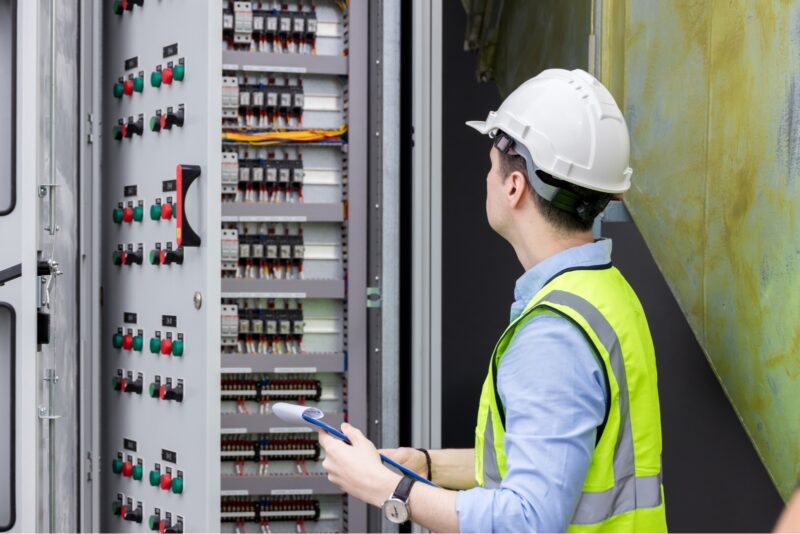
Mechanical Use Cases
Fabric Maintenance – Insulation
This use case involves inspecting and maintaining insulation on equipment or piping to protect against heat loss and prevent underlying damage. It typically includes identifying compromised areas, making necessary repairs or replacements, and ensuring insulation integrity for safe, efficient operations.
Fabric Maintenance – NACE/AMPP/Coating
Fabric maintenance following the standards laid down by the Association for Materials and Performance or AMPP (previously NACE) ensures that protective layers on surfaces meet required standards for corrosion prevention. This typically involves thorough surface preparation, correct coating application, and a final inspection to verify compliance with established guidelines.
AICIP/Corrosion
Assessing and managing corrosion risks to maintain structural integrity and compliance with AICIP standards. Focuses on inspecting corrosion-prone areas, evaluating material degradation, and implementing protective measures.
Non-Destructive Testing (NDT)
Focuses on detecting flaws in pressurised vessels and piping systems using techniques that do not alter or damage the equipment. It helps identify cracks, corrosion, and other issues early, ensuring safety and compliance with relevant standards. Techniques can include Dye Penetrant Testing, Eddy Current Testing, Ultrasonic Thickness, Magnetic Particle Testing, among others.
Registered Plant Inspections
A Registrable Plant is defined as any boiler, crane, hoist, lift or pressure vessel. It includes fixed and itinerant plants like elevating work platforms (EWP), pressure vessels, bridge and gantry cranes, mobile cranes, lifts and hoists, vehicle hoists, monorails, mancages and boilers.
Typical work health and safety regulations state that asset owners must perform maintenance, inspection, and testing of plants regularly.
Rotating Equipment
This use case involves the periodic inspection and maintenance of rotating machinery, such as pumps or compressors. The focus is on identifying early signs of wear, leaks, or mechanical instability that could compromise performance or safety.
Acoustic Emissions
Acoustic Emissions is a non-destructive testing method that detects high-frequency stress waves released by cracks or defects in materials. By monitoring these sound waves in real time, inspectors can locate and assess damage early, helping to prevent structural failures.
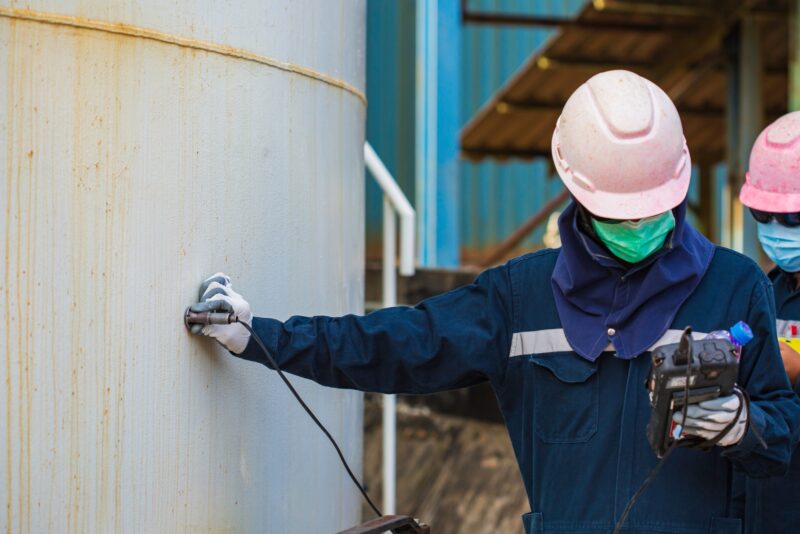
Pressure Equipment
Vessels
Pressure vessels store gases or liquids under high pressure and are subject to strict regulatory standards. Regular inspections focus on verifying vessel integrity, identifying corrosion or damage, and ensuring operational safety.
Piping Loop
Similar to vessels, involves the inspection, testing, and verification of piping loops carrying pressurised fluids to ensure they meet critical standards. Inspections focus is on identifying and addressing integrity threats, such as corrosion, leaks, or stress-related issues, to maintain reliable operation.
Pressure Safety/Regulating/Relief Valves
This use case focuses on ensuring that pressure safety, regulating, and relief valves are fully functional under various operating conditions. It aims to verify each valve’s ability to maintain safe system pressures and promptly address any risk of overpressure or equipment failure.
Small bore tubing
Inspecting and maintaining small bore tubing to ensure leak-free operation and structural integrity. Focuses on identifying fatigue, improper fittings, and potential failures that could compromise system performance.
Hose inspections
Hose registers and inspections involve maintaining details of and verifying hose condition for leaks, structural integrity, and compliance with pressure ratings. These checks help prevent failures that could compromise safety and disrupt operations.
Flange/Valve Management
Inspecting and maintaining flanges and valves to ensure proper sealing, pressure containment, and operational reliability. Focuses on detecting leaks, assessing wear, and verifying compliance with safety standards.
Lifting Equipment
Pad Eyes
Inspecting pad eyes to verify structural integrity, load-bearing capacity, and compliance with lifting safety standards. Focuses on detecting wear, corrosion, and defects to prevent failures during lifting operations.
Containers
Lifting Equipment for Containers is used to safely move, position, and store large cargo or shipping containers. This use case focuses on verifying equipment capabilities, load-bearing capacity, and compliance with relevant safety standards to prevent accidents and maintain operational efficiency.
Cranes & Hoists
Similar to Registrable plant inspections, lifting equipment such as cranes and hoists must be regularly inspected to prevent mechanical failure and ensure compliance. This use case involves verifying structural integrity, load capacity, and adherence to safety regulations.
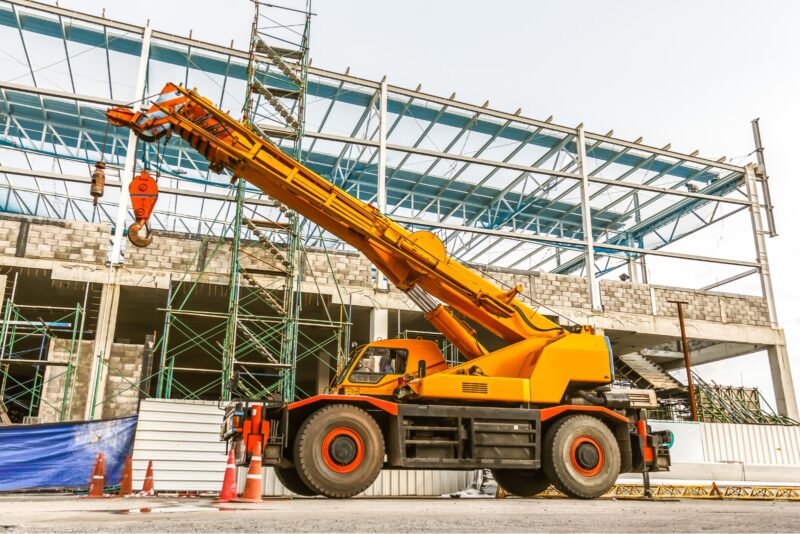
Structural
Visual Inspections
Focuses on the external, visual assessment of structural elements such as beams, columns, and supports. The aim is to detect signs of damage, corrosion, cracking, or deformation that could compromise overall integrity.
Handrails, Ladders & Platforms
This use case involves verifying that handrails, ladders and support platforms meet structural and safety standards to protect personnel from falls and other hazards. It includes checking for proper installation, secure fastening, and compliance with height and load requirements.
Concrete structures
Focuses on assessing the integrity and condition of concrete structures, including foundations, walls, beams, and columns. It typically involves identifying cracking, spalling, corrosion, or other forms of deterioration to ensure continued structural performance and safety.
Jettys (Wharf Safety Compliance Assurance Model)
Also referred to as WSCAM, focuses on ensuring the structural integrity and safety compliance of jetties or wharfs used in maritime settings. It involves routine inspections, hazard identification, and records of remedial actions to maintain safe operations.
Walls
Structural Walls involve assessing the integrity, alignment, and overall condition of load-bearing or partition walls. This may include examining for cracks, moisture issues, or any other defects that could compromise safety and performance.
Commissioning
ITRs
Commissioning is the final phase of a project where systems and components are verified to meet operational requirements. ITRs (Inspection and Test Records) document the checks, measurements, and validation results, serving as proof that everything is installed and functioning correctly before handover.
Preservations
During commissioning, preservations safeguard newly installed equipment from damage or deterioration until final startup. This involves verifying and maintaining protective measures such as coatings, packaging, and environmental controls to ensure readiness for operation.
Factory Acceptance (FAT)
This use case involves testing newly manufactured or procured equipment in a controlled environment before it is shipped to the project site. The goal is to confirm compliance with design specifications, identify potential defects, and ensure performance requirements are met.
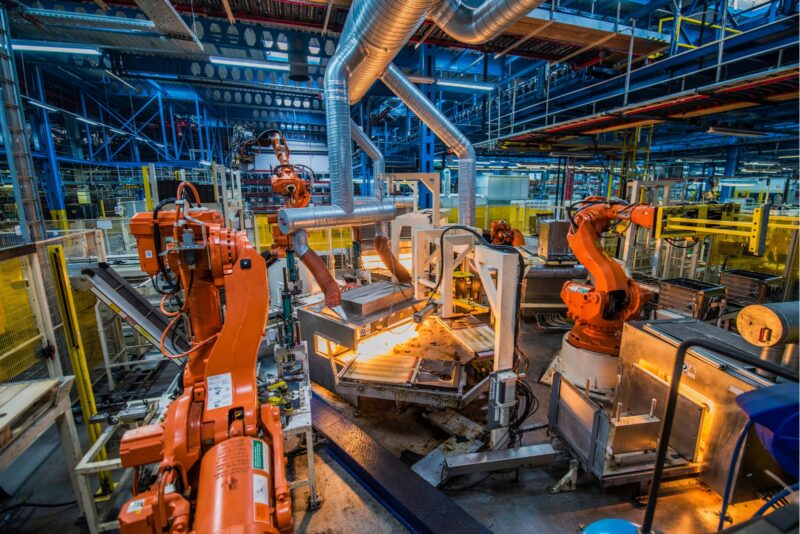
Others
3rd Party Equipment (onshore, receipt, commissioning, decommissioning, demob)
Inspecting and managing third-party equipment throughout its lifecycle, from receipt to decommissioning. Focuses on verifying compliance, functionality, and safety standards at each stage of deployment and retrieval.
Helideck inspections
Inspecting helidecks to ensure compliance with safety regulations, structural integrity, and operational readiness. Focuses on assessing surface conditions, lighting, firefighting equipment, and load-bearing capacity to support safe helicopter operations.
Surveys (e.g., lighting, cable tray, environmental)
Surveys collect data on specific on-site elements such as lighting, cable trays, or environmental conditions. They help confirm safety, functionality, and compliance while identifying any areas needing improvement.
Vehicle prestarts
Vehicle prestart checks involve inspecting a vehicle’s critical components — such as brakes, lights, and fluid levels — before operation. This quick assessment helps identify potential issues early, reducing the risk of breakdowns or accidents.
Accommodation
Inspections and surveys of employee living spaces. It encompasses planning, furnishing, compliance, and occupant well-being throughout the facility’s lifecycle.
Time usage modelling
Analysing time allocation across tasks to optimise efficiency and resource utilisation. Focuses on identifying bottlenecks, improving workflow productivity, and enhancing operational planning.
Streamline Inspections with a Smarter, Digital Solution
Inspection management is more than compliance — it’s about efficiency, data integrity, and proactive risk management. With complex use cases, asset owners need a centralised, digital solution to streamline workflows, enhance safety, and ensure regulatory compliance.
The Inspectivity Platform is purpose-built to handle the complexities of inspection management, offering real-time collaboration, structured data capture, and powerful analytics. Whether you’re managing hazardous area inspections, pressure equipment, or structural integrity checks, our digital inspection solution provides the tools to standardise workflows, enhance safety, and streamline asset lifecycle tracking. Ready to move beyond traditional inspection challenges? Contact us today to see how Inspectivity can transform your inspection processes.