What is RBI?
Risk-Based Inspection (RBI) is a strategic approach focused on managing risks linked to equipment failure. It combines risk assessment with traditional inspection and maintenance to determine optimal inspection intervals, based on failure probability and consequences. This process considers safety, economic, and environmental impacts, aiming to keep failure risk below acceptable limits. RBI ensures compliance with safety and environmental standards while enhancing operational efficiency by targeting resources effectively.
RBI and its origins
RBI emerged in the late 1980s as industries sought efficient ways to manage asset integrity amid increasing safety and regulatory demands. Initially developed for the oil and gas industry, it has expanded to sectors like petrochemical, power generation, and pharmaceuticals. The American Petroleum Institute (API) formalised the first standards, API 580 and API 581, providing a framework for risk-based inspection systems. These guidelines standardised practices and elevated RBI from a niche concept to a key component of industrial asset management.
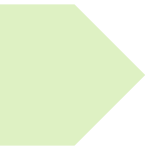
API 580 vs API 581
Though API 581 complements the existence of API 580, they actually provide different guidelines. API 580 focuses more on risk-based inspection, while API 581 focuses on asset integrity management by measuring through calculation. Learn more.
RBI objectives and process
RBI aims to enhance safety and reliability, optimise maintenance, and reduce costs. By focusing on high-risk areas, organisations can prevent failures, extend asset life, and improve overall performance, aligning with the goals of ensuring safety, compliance, and efficiency.
The RBI process starts with a thorough assessment of equipment to identify potential failure modes and the risks they pose to operations, safety, and the environment. Key steps include:
- Identification of Failure Modes: Review the history, operating conditions, and past incidents to identify likely failure scenarios.
- Risk Assessment: Assess the probability and consequences of each failure mode, typically using a risk matrix to categorise risks.
- Development of Inspection Plans: Create customised inspection and maintenance schedules based on risk assessments. High-risk equipment requires more frequent inspections, while lower-risk equipment can have longer intervals.
- Implementation and Monitoring: Carry out inspections, monitor results, and analyse changes in the risk profile. This dynamic process allows for continuous improvement and updating of plans as conditions change.
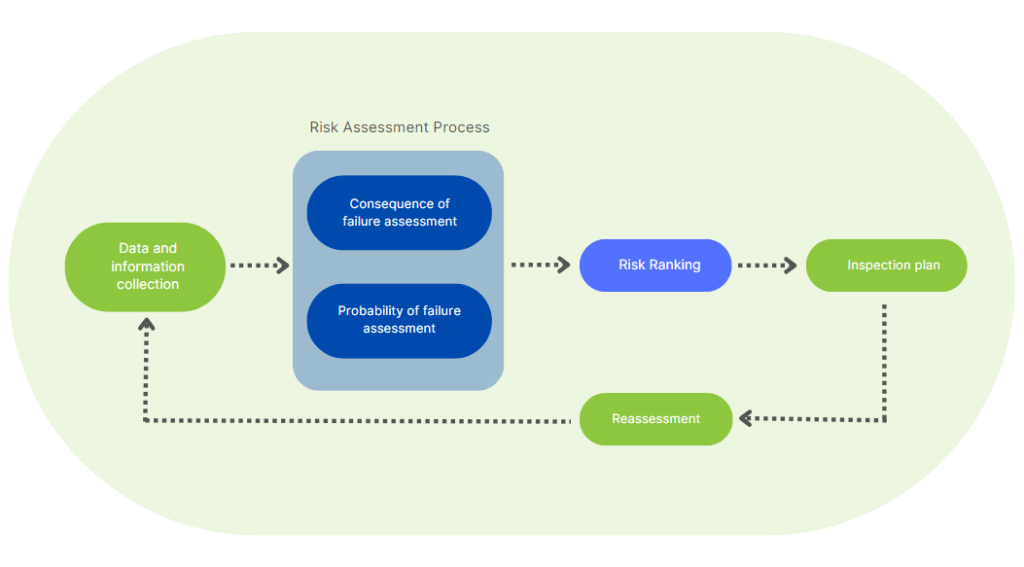
How Risks are Identified and Quantified?
Risk assessment is the foundation of RBI. It involves a systematic approach to identifying potential equipment failure risks, quantifying them, and prioritising inspection efforts. Key steps include:
- Data Collection: Gather comprehensive data on equipment design, operating conditions, historical performance, and maintenance history.
- Failure Mode Identification: Analyse data to identify possible failure modes, understanding how and why equipment could fail.
- Probability Assessment: Estimate the likelihood of each failure mode occurring, considering current conditions and historical data.
- Consequence Analysis: Evaluate potential impacts of each failure mode, including safety hazards, environmental damage, and production losses.
- Risk Calculation: Combine probability and consequence assessments to calculate overall risk, often expressed numerically or categorised into risk levels.
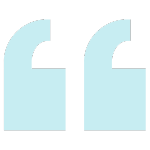
An inspection task should be perceived as an opportunity to get a more accurate quantification of the damage present in the component so risk management can take place. Victor Borges, DNV
Risk Matrices and Their Role in RBI
Risk matrices are essential for visualising and categorising risks. A typical matrix classifies risks by their likelihood and severity, aiding quick decision-making.
- Prioritisation: Highlighting high-risk equipment for immediate attention.
- Consistency: Providing a standardised method for assessing risks across various units.
- Communication: Facilitating discussions about risks among different organisational levels.
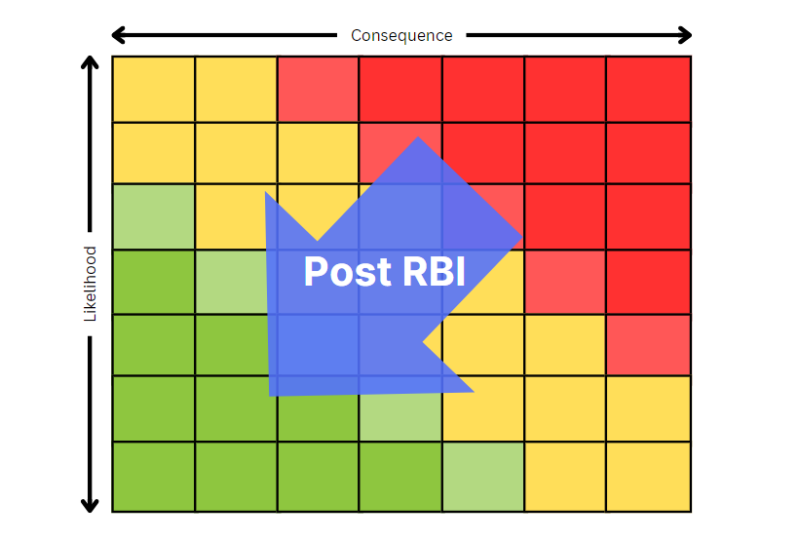
Importance of Data and Data Quality
Reliable RBI outcomes depend on high-quality data. Accurate, timely, and comprehensive data is crucial for:
- Precision in Risk Evaluation: Ensuring more precise risk evaluations for effective prioritisation.
- Confidence in Decision Making: Building confidence in risk assessment results and subsequent decisions.
- Adaptability and Responsiveness: Allowing quick adaptation of strategies in response to changing conditions or new information.
- Compliance and Reporting: Meeting regulatory requirements and thorough documentation for audits.
For engineering teams, robust risk assessment, effective use of risk matrices, and prioritising high-quality data acquisition enhance operational safety, optimise maintenance costs, and improve asset performance. Implementing these core principles supports business continuity and corporate reputation.
Applications of RBI in Industry
Electrical Equipment for Hazardous Areas (EEHA)
RBI is crucial for managing the integrity and safety of electrical equipment in hazardous areas (EEHA), where explosive atmospheres may exist. RBI helps prioritise inspections based on failure risk and consequences like explosions or fires. Key aspects include:
- Targeted Inspections: Identifying critical components that might ignite explosive atmospheres and prioritising them for frequent and detailed inspections.
- Compliance and Safety Enhancements: Ensuring compliance with international safety standards such as ANZEx, IECEx, ATEX, and NEC 500, thus enhancing overall safety.
- Optimised Maintenance: Focusing resources on high-risk areas to optimise maintenance schedules, reducing downtime, and extending equipment life in hazardous environments.
If you are interested in developing an RBI strategy for EEHA, then an important reference is the Guidelines for managing ignition risk by inspection of Ex Electrical equipment in hazardous areas.
Pressure Equipment: Boilers, Pressure Vessels, and Piping Systems
RBI is essential for pressure equipment in industries like oil and gas, chemicals, and power generation due to the risk of catastrophic failures. Key aspects include:
- Failure Mode Analysis: Identifying potential failure modes like corrosion, erosion, or mechanical wear, and their likelihood and consequences.
- Inspection Scheduling: Scheduling inspections based on risk assessments to ensure high-risk equipment is inspected more frequently than lower-risk assets.
- Lifecycle Management: Providing insights for better lifecycle management of pressure equipment, aiding in repair, replacement, or retirement decisions.
Novel Applications
RBI is also applied in civil infrastructure, marine, and aerospace sectors, demonstrating its versatility:
- Civil Infrastructure: Prioritising maintenance of bridges, tunnels, and water treatment facilities based on failure risk and impact on public safety.
- Marine: Assessing the structural integrity of ship hulls to detect and monitor system, sub-system, equipment and component degradation and applying appropriate decision making criteria to manage risk to acceptable levels.
- Food: Risk-based food inspection, as opposed to traditional food inspection, provides opportunities to build systems to prevent food safety incidents by identifying risk factors and assessing the effectiveness of control measures in place.
For engineering teams, applying RBI across these sectors (and many others) supports a disciplined, data-driven approach to maintenance and safety management, enhancing operational reliability, safety, and compliance with industry-specific regulations and standards.
Benefits of Implementing RBI
Enhanced Safety and Reduced Risk of Equipment Failure
Implementing RBI enhances safety by systematically managing equipment failure risks. This proactive approach includes:
- Predictive Maintenance: Shifts from reactive to predictive maintenance, preventing failures before they occur.
- Safety Culture: Promotes safety awareness across the organisation, integrating safety considerations into daily operations.
- System Reliability: Focuses on high-risk areas, ensuring critical components receive necessary attention.
Cost Savings Through Optimised Inspection Schedules
RBI prioritises inspections based on risk, leading to significant cost savings:
- Resource Allocation: Allocates resources effectively by focusing on high-risk equipment.
- Extended Equipment Lifespan: Identifies issues early, reducing repair costs and extending equipment life.
- Reduction in Unplanned Downtime: Manages risks to reduce unplanned shutdowns, maintaining productivity.
Compliance with Industry Standards and Regulatory Requirements
RBI aids compliance with regulatory standards and industry best practices:
- Regulatory Adherence: Ensures operations meet strict safety and environmental standards through systematic risk management.
- Best Practices: Demonstrates commitment to leading safety and maintenance practices.
- Audit Readiness: Provides comprehensive documentation for audits, showing due diligence and operational integrity.
For engineering teams, RBI enhances safety, reliability, and compliance, driving efficiency and aligning with business goals.
Risks and Challenges of RBI
Limitations of Data Quality and Availability
A fundamental challenge in RBI is the reliance on high-quality, comprehensive data about equipment history, maintenance records, and failure modes. Main concerns include:
- Inadequate Data Infrastructure: Historical data may be incomplete, inconsistently recorded, or inaccessible due to outdated systems.
- Data Integrity Issues: Errors in data entry, delays in updates, or inadequate capture practices can lead to inaccuracies in risk assessments.
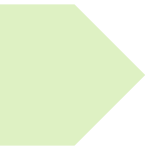
Without solid data, assessments may overly rely on expert judgments, introducing bias or inconsistency.
Potential for Over or Underestimation of Risks
RBI depends on accurate risk models to predict failures and consequences. Incorrect assumptions or model inaccuracies can lead to:
- Overestimation of Risk: This results in unnecessary inspections and maintenance, wasting resources and disrupting operations.
- Underestimation of Risk: Leads to insufficient monitoring and maintenance, increasing the likelihood of unexpected failures and associated impacts.
Integration Challenges with Existing Maintenance Systems
Integrating RBI with existing systems presents several challenges:
- System Compatibility: Existing systems may not be compatible with new RBI software, requiring costly customisation or replacement.
- Change Management: Implementing RBI involves significant procedural and workflow changes. Resistance to change can hinder integration.
- Continuous Updating: RBI requires continuous updates as new data becomes available and conditions change. Ensuring synchronisation with real-time data is crucial.
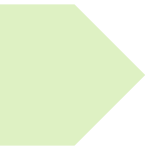
Implement advanced data management technologies like digital inspection management for higher data quality and accessibility.
Mitigation Strategies
To address these challenges, engineering managers can adopt strategies such as:
- Enhancing Data Management Practices: Improve data collection, storage, and analysis capabilities. Implement advanced data management technologies like digital inspection management for higher data quality and accessibility.
- Model Validation and Regular Reviews: Regularly review and validate risk models to ensure accuracy and adjust them based on new information.
- Comprehensive Training and Change Management: Conduct comprehensive training sessions and implement a robust change management strategy to address resistance and promote acceptance of new practices.
Understanding these challenges is crucial for successful RBI implementation. Proactively addressing these risks enhances the reliability and effectiveness of RBI programs, safeguarding operations and improving performance.
What’s next for RBI?
Advanced Technologies
Standard RBI methodology depends on two types of assessment, screening and then a more detailed assessment. Screening aims to establish the critical elements (e.g., equipment) in asset-intensive industries that should have the main focus when it comes to detailed assessment. Typically screening is a qualitative assessment, based on the subjective viewpoints of experts and their interpretation of data. The outcome is to identify which assets and systems warrant further detailed assessment. We have already discussed the risks associated with poor screening. We have also mentioned several mitigation strategies but how can advanced technologies assist such artificial intelligence (AI) and machine learning (ML)?
The key benefit is in the pre-screening phases of RBI. This phase is reliant on the analysis of large amounts of data, and (typically) unstructured information. With outcomes determining which assets should be monitored more frequently and in more detail.
Rather than leaving this decision to domain experts, organisations can now leverage AI language models to process data to perform a pre-screening. A new concept called Retrieval-Augmented Generation, aka RAG, is leading the charge.
“Retrieval-Augmented Generation (RAG) is the process of optimizing the output of a large language model, so it references an authoritative knowledge base outside of its training data sources before generating a response.” (AWS)
RAG complements and improves a large language model (LLM) to provide a more authoritative answer. For RBI this means we can vastly improve the pre-screening by passing historical technical information to the LLM to help us more clearly understand where our asset risks lie. Further optimising resources, lifetime and safety of critical assets.
Role of Inspection Data
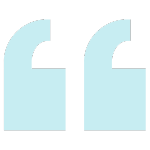
As highlighted in recent discussions on the challenges of AI and machine vision in risk-based visual inspections, the scarcity and quality of training data can significantly impede the development and effectiveness of AI models.
Further to our discussion above on RAG, one of the key advantages over alternative AI approaches is its ability to continuously refresh its knowledge of the key parameters. In the background, the model is continuously creating new or updating existing technical data as it becomes available. For example via a digital inspection solution, a continuous supply of updated strongly typed condition data, photographs or inputs from external sources such as sensors can be fed to the model. Further strengthening the risk calculation for ongoing detailed analysis.
Inspectivity and RBI
Inspectivity’s platform is more than just a tool for asset management; it’s a strategic partner in maximising asset performance. Through its focus on data collection and real-time asset tracking, Inspectivity empowers organisations to optimise their asset performance via RBI and artificial intelligence, ensuring operational excellence and long-term sustainability.
If you are ready to discover Inspectivity’s asset management capabilities, explore our plans and pricing or schedule a demo today.