In Part 2 of our series on Risk-Based Inspection (RBI), we delve into the critical aspects of managing Electrical Equipment in Hazardous Areas (EEHA). This article explores the key components of an effective RBI strategy tailored for EEHA, highlighting the integration of advanced inspection methodologies that enhance safety and compliance. We will also introduce the new capabilities of Inspectivity Platform SaaS, including our dedicated RBI module designed to streamline inspection processes and improve overall operational efficiency.
EEHA
Electrical Equipment in Hazardous Areas (EEHA) refers to electrical systems and devices installed and operated in environments where explosive atmospheres may be present, such as in industries like oil and gas, mining, and chemical processing. These hazardous areas are classified based on flammable gases, vapours, or dust, which can ignite if exposed to sparks, heat, or malfunctioning equipment. EEHA requires specialised design, installation, and maintenance practices to ensure safety, prevent accidents, and maintain operational integrity. Compliance with stringent international standards such as IECEx, ANZEx, ATEX, and NEC 500 is essential to achieving these goals.
Typical EEHA Framework
The key components of an Electrical Equipment in Hazardous Areas (EEHA) strategy include:
- A documented, implemented, and regularly reviewed policy for managing electrical equipment at your facilities.
- Competent personnel, including a Technical Authority, an Audit Team, and suitably qualified Internal and Contractor Inspector Teams.
- Inspections, which cover various grades, such as Initial, Visual, Close, and Detailed inspections, including:
- Inspections of new installations.
- Periodic inspections.
- Sample inspections, typically using two sampling methods:
- Progressive sampling: A random sample of the total population is inspected (e.g. 10%). If further inspection is needed, another random sample (e.g. 10%) is taken from the remaining population. The remaining population (e.g. 80%) is inspected if a third round is required.
- Random sampling: A sample is selected randomly from the entire population for each inspection iteration. This can lead to the reinspection of the same assets, which may seem duplicative but can be advantageous in identifying issues such as maintenance-induced problems.
- Opportunistic inspections, such as during equipment breakdowns.
- Risk-based inspections, where electrical equipment is assessed for ignition risk, grouped into homogeneous lots, and inspected using a sampling strategy.
- Key performance indicators (KPIs) to monitor the overall health and effectiveness of the system.
EEHA & RBI
Implementing a 100% detailed inspection of your electrical equipment may seem like the EEHA inspection strategy that offers the highest confidence in delivering safe outcomes. However, this approach is extremely time-consuming and often impractical with the resources available. It also carries the risk of introducing safety issues during maintenance. As an alternative, combining periodic and opportunistic inspections with an RBI sampling methodology offers greater assurance in the integrity of equipment while being significantly more cost-effective.
To support companies adopting an RBI approach, the Energy Institute of London has produced a set of guidelines. These guidelines provide detailed insights for developing a streamlined sampling methodology and serve as a focal point for managing risk.
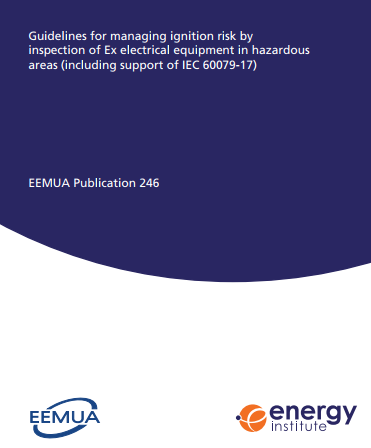
The guidelines provide a general framework for Ex inspections, along with specific details on how to implement an RBI sampling strategy. Developed by the Energy Institute’s electrical committee – which includes senior electrical engineering experts from some of the world’s largest petrochemical and inspection companies – the guidelines are designed to help organisations meet the complex demands of EEHA compliance.
The approach for establishing an RBI sampling strategy is based on ISO 2859-1, the international standard for inspection guidelines, combined with the EEHA requirements of IEC 60079. Key areas covered include EEHA management practices, setting up an effective RBI sampling methodology, and the specific electrical concepts relevant to EEHA compliance.
Important Prerequisites
The Energy Institute guidelines enable facilities to establish an inspection methodology that tailors the level of inspection to the ignition risk, helping to reduce the chances of introducing additional risks through intrusive maintenance. This approach is not only safer but also highly cost-effective.
While the benefits of implementing risk-based inspection and enhanced EEHA management are clear, the guidelines set out strict prerequisites that must be met before adopting an Ex RBI approach. These prerequisites include:
- A complete equipment register.
- High-quality historical inspection data.
- A robust maintenance management system with a systematic approach to auditing and review.
Operators of critical infrastructure may need to continue with a conventional EEHA strategy until these prerequisites are fully in place.
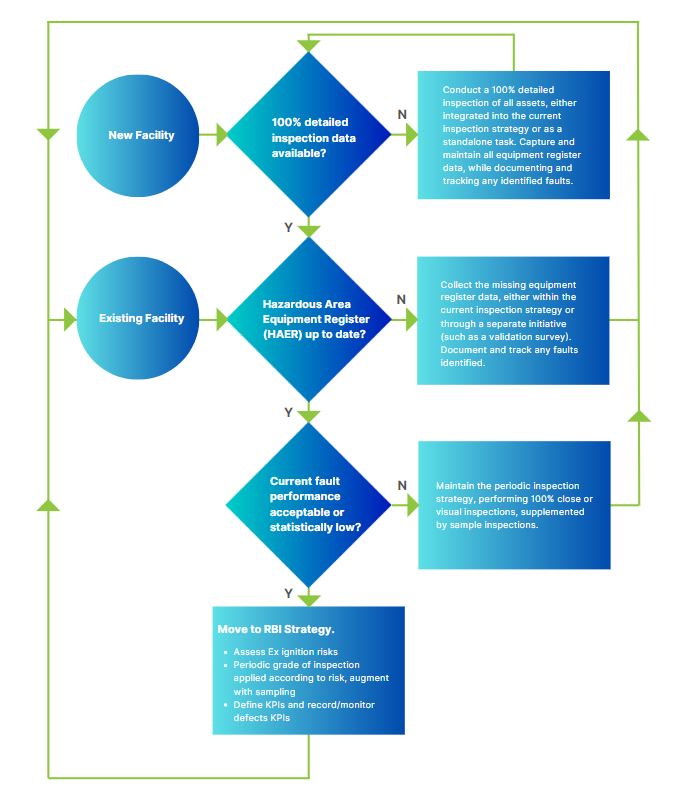
EEHA RBI Methodology
The foundation of a robust RBI strategy for managing hazardous area equipment lies in proactive risk management and strict compliance with safety standards. This approach not only enhances the reliability and safety of electrical equipment but also optimises inspection and maintenance schedules, aligning them with the facility’s operational risk profile to ensure maximum efficiency.
The development of an RBI methodology based on the Energy Institute guidelines involves several key elements. These are outlined at a high level below, but for more detailed information, please refer directly to the guidelines.
Equipment Register
The equipment register is a comprehensive database of equipment records that includes a minimum set of fields to identify each item’s location, technical parameters, Ex classification, age, and environmental data. This information is crucial for tracking and managing the equipment effectively within hazardous areas.
Lots
The sampling methodology outlined in the Energy Institute guidelines, based on ISO 2859, assumes that equipment can be grouped into homogeneous units, or “Lots.” However, this can be challenging for electrical equipment, as it typically involves different protection concepts, exposure to various environments, and placement in locations with differing hazardous area risk levels.
To address these challenges, the guidelines recommend grouping equipment based on three key parameters:
- Hazardous Area Classification
- Type of Protection
- Environmental Conditions
When developing Lots using these parameters, it’s important to remain mindful of practical application. Lot design should consider how it aligns with the development of workpack scopes. If your RBI Lots do not account for practical inspection factors, such as location details, your sampling strategy may still require significant work order preparation.
RBI Strategy
Grade of Inspection
Before electrical equipment is commissioned for service, the grade of inspection should always be classified as Detailed. In contrast, for periodic or RBI sampling inspections, the grade will be a combination of Detailed and Close inspections. The ratio of Detailed to Close inspections will be determined by the Equipment Risk, which is assessed based on ignition risk (the probability of a source of ignition versus the probability of a flammable atmosphere) and the hazardous area classification (Zone 0, 1, or 2).
Each Lot may group equipment with similar Equipment Risk levels, meaning that different Lots may require varying proportions of Close and Detailed inspections. This variation will also influence the resourcing requirements for work preparation.
Sample Size and Rejection Criteria
Once Lots are defined, you can develop sampling plans based on the sample size of each Lot, which refers to the number of random equipment items to be inspected.
To determine the required sample size, two aspects need to be evaluated: the size of the Lot and the category of inspection, which indicates the level of effort that should be applied (reduced, normal, or increased) to the inspection of the Lot.
The degree of effort is determined by assessing the Equipment’s Criticality, which is influenced by ignition risk and the severity of the environment.
By combining the category of inspection with the Lot size, you can then establish the appropriate rejection criteria for a sample, meaning the allowable number of faulty items found within that sample.
For more details on this process, please refer to the Energy Institute Guidelines.
Frequency of Inspection
The IEC 60079 standard recommends that the maximum interval between inspections should not exceed three years. However, you may choose to shorten this period for individual Lots based on factors such as ignition risk and the specific environment in which the equipment operates.
Credited Inspections
EEHA inspections will also be conducted outside of RBI campaigns as part of scheduled maintenance and equipment overhauls or repairs. These inspections can be credited toward the RBI sample sizes within the affected Lots.
Performing Inspections
Fault Score
EEHA inspections are conducted to identify faults in electrical equipment. A weighted scoring system is essential, as a single piece of equipment may have multiple faults, each with varying levels of ignition risk. This system allows for an assessment of the overall “faultiness” of individual equipment and its contribution to the total fault score for the RBI sample.
The EEHA inspection checklist should document the outcomes of various condition assessments, with each assessment question focusing on one of three areas:
- Safety
- Integrity
- Housekeeping
In conjunction with ignition risk and the categories mentioned above, fault scores are assigned to the identified action items or faults, as follows:
Probability of Ignition of Faulty Equipment | Zone 2 | Zone 1 | Zone 0 |
Low (Housekeeping) | 0.25 | 0.25 | 0.25 |
Medium (Integrity) | 0.25 | 0.5 | 1 |
High (Safety) | 0.5 | 1 | 1 |
When a piece of equipment has multiple faults, all are recorded, but only the most severe fault is considered when determining the aggregated fault score for the RBI sample set.
Accept / Reject Samples
Remedial actions are determined by the weighted fault score and whether the Lot meets acceptance criteria. If the failure rate is below the accepted fault score, the Lot is accepted; if it exceeds the fault score, the Lot is rejected, necessitating further analysis.
Rejected Lot: The guidelines stipulate that the causes of faults must be identified through an audit. If a common failure mode is detected, the faulty equipment is deselected, and a new sample is inspected. If no common failure mode is identified, the faulty equipment remains in the Lot, and a second sample is inspected. If the combined score of both inspections is less than twice the fault score, the Lot is deemed acceptable. If the Lot is still considered unacceptable, it must undergo a full inspection or justification, which may trigger stricter inspection protocols.
Accepted Lot: The causes of any faults are identified. If a common failure mode is found, additional equipment may require inspection and repair.
Any necessary repairs are prioritised based on the severity of the faults identified within the Lots and the criticality of the faulty equipment. Faults are classified by severity (Safety, Integrity, Housekeeping), ensuring that urgent issues are assessed and addressed promptly to mitigate any impact on safety or operations. The EEHA database should track and record the lifecycle of faults along with the corrective actions taken.
Inspectivity Platform SaaS
Implementing a robust Risk-Based Inspection (RBI) strategy is crucial for ensuring compliance and safety in managing Electrical Equipment in Hazardous Areas (EEHA). By leveraging the principles outlined in the Energy Institute guidelines, organisations can significantly enhance their inspection processes while effectively mitigating risks associated with equipment failures.
We are pleased to announce that the Inspectivity Platform SaaS now includes an advanced RBI module specifically designed for EEHA. Key features of this module include:
- Lot Management: Streamlined organisation of equipment into homogeneous lots for effective sampling and inspections.
- Out-of-the-Box RBI Strategy: Ready-to-use RBI strategies, along with support for custom strategies tailored to specific organisational needs.
- RBI Run Manager: A user-friendly interface that simplifies campaign planning, work preparation, and outcome monitoring.
- Automated Fault Scoring and Lifecycle Management: Effortlessly manage faults and track their lifecycle to enhance inspection accuracy.
The introduction of this support for risk-based inspection further strengthens Inspectivity’s position as a best-in-class solution for regulatory compliance, as well as for any asset-centric inspection use case.
If you are interested in learning more, we invite you to request a demonstration and discover how our solution can transform your EEHA management processes.